Enercon Plasma Treater is a Game Changer for Biovation Labs’ FDA – Approved Packaging
Biovation Labs is an NSF 455-2 registered facility, providing their high-quality formulation, blending, encapsulation, tableting, and packaging. As a certified cGMP (Current Good Manufacturing Practices) facility, Biovation Labs takes pride in its manufacturing and packaging capabilities for all types of nutritional supplements. Their meticulous quality approach extends to every part of the operation, from the raw materials sourced for products to the ink used on the bottom of the bottles being packaged.
“Our experience with Enercon was game-changing and helped optimize the process by improving the quality of the finished product and reducing rework.”
All products produced at Biovation Labs are printed with lot codes produced by inkjet printers. These codes are essential to both the manufacturer and consumer; without a legible lot code, the traceability required by the FDA would not be in place and containers must be returned and reworked by the manufacturer. Biovation hit a snag in their otherwise seamless operations when they discovered the ink for the required lot code was rubbing off during shipment to customers. The returns meant customers had to wait for a replacement shipment. It also meant Biovation Labs had to incur additional costs and lost time on rework. Finding a solution to this challenge was imperative.
Finding the Root Cause Led to a Plasma Solution
Royce Downard, Biovation’s Maintenance Manager, conducted a detailed root cause analysis. His team found the issue was 100% contained to the HDPE bottles used for packaging (other plastic-type bottles did not have the same problem). Non-porous plastic surfaces are inherently inert with low surface energy and limited bonding sites, making plastics hydrophobic and presenting printing challenges. In this case, an additional element was at play. The HDPE bottles also incorporated a release agent as part of their molding process. The release agent would rise to the bottle surface and prevent a strong ink bond during the printing process.
Biovation Labs learned of Enercon’s plasma solutions through a trade show. Plasma is the fourth state of matter. Enercon creates a blown-ion plasma discharge by ingeniously applying high voltage across two electrodes and forcing the ions to jet out of a discharge head with high-pressure air. The blown-ion plasma bombards surfaces with a stream of charged ions to clean, etch and functionalize the surface. The goal is to increase surface energy and wettability by removing surface contaminants such as release agents and create additional bonding sites (or surface area for the ink to bond with).
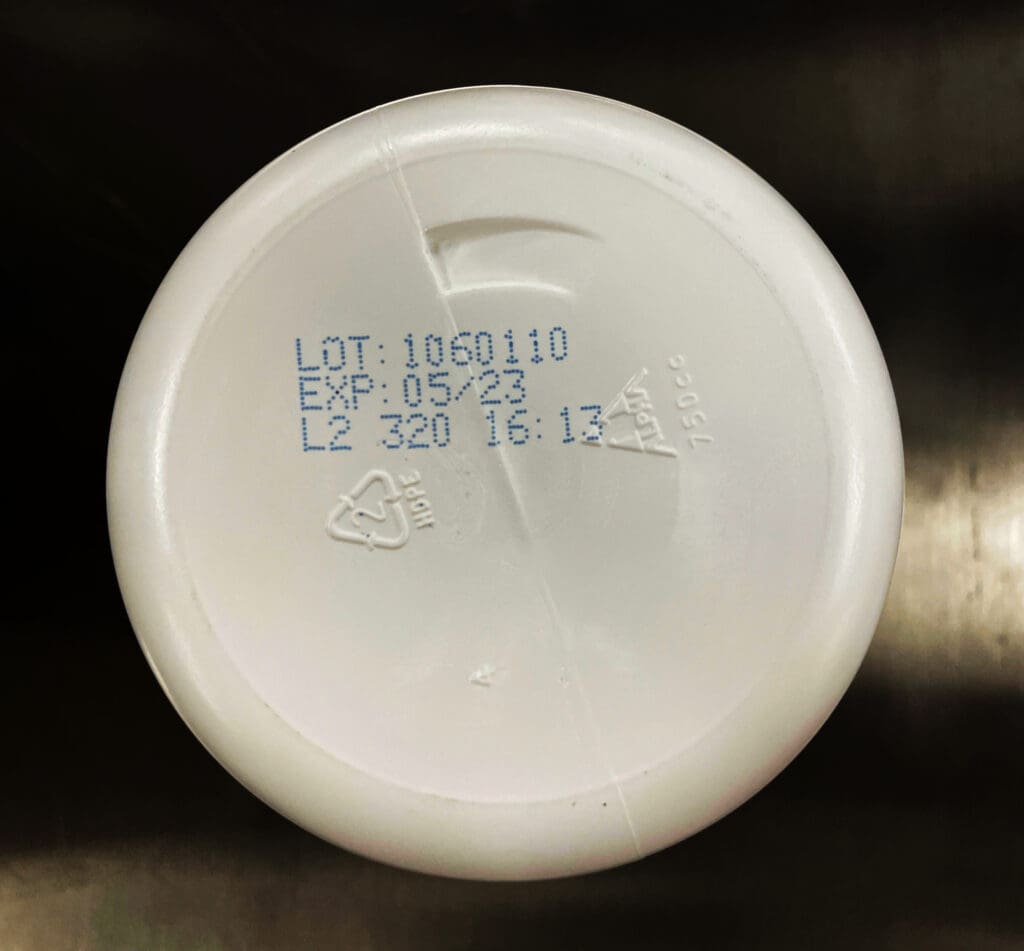
Biovation Labs invested in its first Blown-ion™ Plasma Treater and saw immediate results. “The plasma treater was able to clean off the release agent allowing for proper ink adhesion,” Downard notes; “We saw an immediate decrease in rework related to lack of ink adhesion and illegible lot codes.”
“We chose the Enercon Blown-ion Plasma Treater due to its compact size, ease of operation, cost, and availability,” says Downard. Integrating the in-line technology was relatively simple. The discharge heads are mounted beneath the conveyor in an area where the bottom of the bottles is exposed. Bottles receive treatment and then are inkjet printed moments later.
Today, the company owns three Blown-ion™ treaters. “Our experience with Enercon was game-changing and helped optimize the process by improving the quality of the finished product and reducing rework,” concludes Downard.
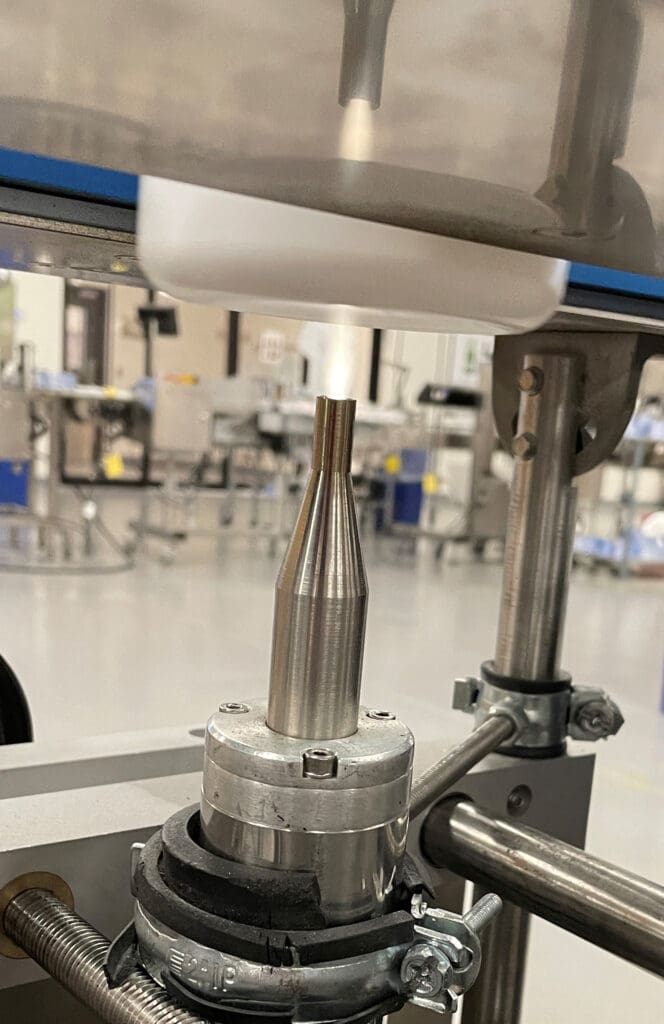