Plasma & Flame Surface Treatment Distance & Dwell Time Recommendations for Consistent Treatment Results
What is the ideal distance between the treatment head and the surface to be treated?
The answer depends on the surface treater you are using and your specific application. However, there are some general guidelines that you should be aware of:
Treatment Distance
- The Blown-arc™ plasma treater is designed to provide optimal treatment with a distance between the treatment head and the surface to be treated of 3/8” – 5/8”
- The Blown-ion™ plasma treater is designed to provide optimal treatment with a distance between the treatment head and the surface to be treated of 1/4” – 1/2”
- The Flame Series Pro is designed to provide optimal treatment with a distance between the treatment head and the surface to be treated of:
- 1” – 3” for a 24 series burner
- 1.5” – 4” for a 226 series burner
- It is sometimes possible to produce acceptable results at slightly greater distances, but a greater dwell time may be required
- For some applications, treatment at closer distances may be successful, but always consult with Enercon prior to attempting.
- Depending on the receptiveness of the surface being treated, it is possible for the effects of treatment to extend beyond the visible spread of the treatment.
Treatment Dwell Time
- Amount of treatment is a function of distance and dwell time
- The slower the treatment head passes over the surface -the greater the dwell time, and in most cases, the higher surface treatment
- Too much dwell time can sometimes damage the treated surface
- Too little dwell time can sometimes result in insufficient treatment
Treatment Angle
- For a flat surface, always start out at a 90-degree angle or perpendicular to the surface to be treated.
- If treating a dimensional object, experiment with a treatment angle that enables the treatment discharge to cover the desired treatment area.
Measuring Treatment Success
- Dyne level testing is a simple way to determine the effects of surface treatment and is a good indicator for chances of adhesion success.
- Contact angle and other tests may also be used to evaluate treatment effectiveness on flat surfaces.
- In most cases, the goal of treatment is to improve adhesion; in some cases, little or no discernible movement in dyne level can still produce successful adhesion. So, it is good practice to always verify that adhesion is successful or unsuccessful rather than rely completely on a dyne level test.
Pretesting and good documentation are the staples of every quality control program. Define your system variables and record the results. If you experience different production line results, you can use your original data as confirmation. In addition, Enercon is always available to provide free application expertise and lab testing.
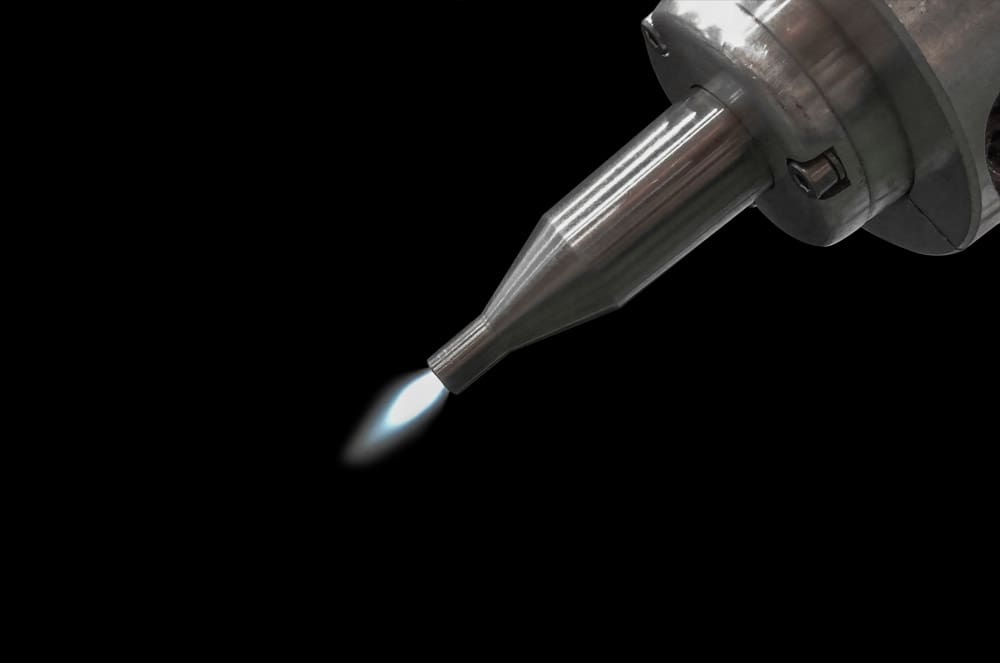