Clean is good, but is it good enough for successful adhesion?
Smart manufacturers recognize the importance of a clean surface when bonding components. If a part is not clean, the adhesive will bond to the surface contamination rather than directly to the surface itself. Manufacturers commonly use a solvent to clean the surface. However, this isn’t always enough to produce the desired adhesive outcome.
A clean surface exposes the surface to be bonded, but it does not take into consideration the inherent surface energy of the material. Every material has a unique surface energy made up of polar and disperse energies. Add these together and you get what is referred to as the ‘Surface Free Energy’ of your material. (The table below shows different materials initial dyne levels and their increased levels after plasma surface treatment.)
Increased Surface Energy Examples | ||
Material | Initial Dyne Level | Post Treatment Dyne Level |
Polycarbonate | 37 | 56-72 |
Polyethylene | 32-34 | 42-60+ |
Polypropylene | 30-34 | 45-60+ |
Polystyrene | 36 | 52-70 |
PTFE | <30 | 50 |
Rigid PVC | 33-36 | 42-60+ |
TPU | 34 | 48 |
In general, the higher this energy, the better your bond strength will be. For example, polypropylene has a very low surface energy and even a clean PP surface may be difficult to bond to without additional surface preparation. Furthermore, while it may be possible to create an adhesive bond, the durability and strength of the bond may be severely limited.
Another barrier to successful adhesion is a lack of bonding sites. The more usable the surface area, the better your overall bond strength will be. This is why some manufacturers will either chemically etch or mechanically roughen a surface prior to bonding. While these methods may be helpful, they do not provide the full complement of surface preparation that plasma and flame surface treating offer.
Plasma and flame surface treatment systems clean, etch and functionalize surfaces in a single pass. They clean your surface by removing organic residue, increasing the bondable surface area up to 30% by micro-etching, and adding functional groups to the outer most molecular layers to promote strong bonds. These hydroxyl or carboxyl groups increase the Surface Free Energy of your material and in most cases will drastically improve your bond strength.
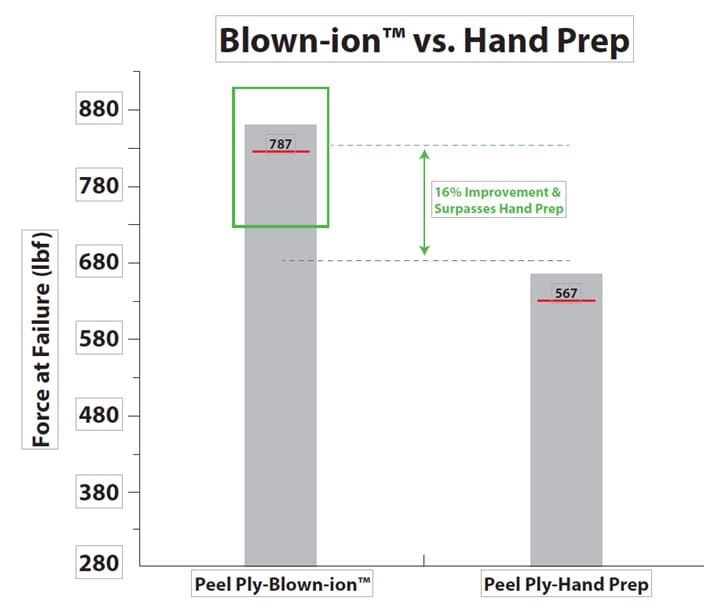
In some cases, using plasma or flame surface treating may eliminate the need for the other surface preparation technologies previously mentioned. In other cases, the addition of plasma and flame may provide a superior result. (The chart above shows a 16% improvement when using a Blown-ion Plasma Treater over hand preparation.)
{Related: What Plasma Treatment Actually Does to a Surface}
The overall goal is to create more consistency in your process: faster throughput and stronger bonds lead to fewer defective parts and overall higher quality. It also makes for much happier customers. Please contact us today to see if plasma or flame is right for your application.
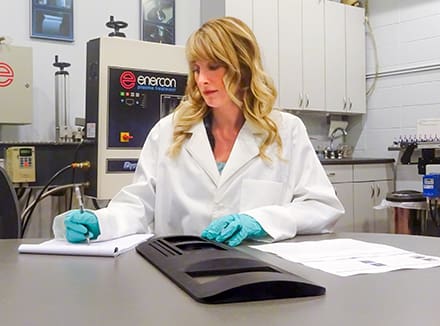