Robotic Plasma Treatment for Headlamp Adhesion
Hella Australia Pty Ltd designs and manufactures automotive lighting equipment, plastic moldings and accessories for the most sophisticated new cars in the world. Throughout their facility is state-of-the-art technology used to supply interior and exterior lighting including: headlamps, reflectors, lenses, and auxiliary lamps.
Hella’s factory is equipped with a wide variety of molding, painting, hot foil stamping, aluminum metallizing and lacquering operations. When Chief Engineer Andrew Meads and his team needed to improve adhesion for a new headlamp assembly, they turned to Enercon.
Toyota Camry Headlamp Project
Hella’s challenge was to improve adhesion on a glue track for Toyota’s newest polypropylene headlamp. A silicone adhesive was to be used to secure a polycarbonate lens. The use of silicone is on the rise for automotive lamps exposed to higher temperatures and stresses for a number of reasons:
- More internal components create more heat
- Halogen and BiXenon bulbs are hot
- Increased temperature behind the lamp
- Styling trends with small lamps and tighter tolerances put more stress on the adhesive
Blown Ion Series air plasma treater
Enercon’s blown ion air plasma surface treater, the Blown Ion Series, proved to be an ideal match for the application. It discharges a high velocity stream of concentrated charged ions to effectively treat a wider variety of materials with an aggressive micro-etching effect.
Andrew’s Mechatronic Engineers integrated the Enercon plasma treatment discharge head into a Motoman 6-axis articulating robotic arm. The robotic arm follows the glue track at the precise speed and air gap required to optimize treatment.
Enercon’s electronic architecture ensures that the treatment discharge is consistent. The system monitors power, voltage, current and frequency to ensure accurate power regulation. The control board uses the latest high speed programmable logic in conjunction with wide bandwidth analog circuitry to measure and control all required parameters.
The combination of precision robotic control and safe guarding electronic architecture provides Hella with the repeatable treatment results required for the headlamp application.
Shorter dwell time increases productivity
Before installing the new Blown Ion Series, Hella used an Enercon blown arc air plasma system. It also performed well, but the upgrade to the new system provided an immediate benefit for Hella. The blown ion system required a shorter treatment dwell time which allows an increase in the speed of the treatment process.
Hella purchased a second Blown Ion Series treater for another line dedicated to the assembly of headlamps. More importantly, Hella’s efforts have been recognized by Toyota. A few years ago, Hella Australia won Toyota Australia’s Excellence Award for Engineering.
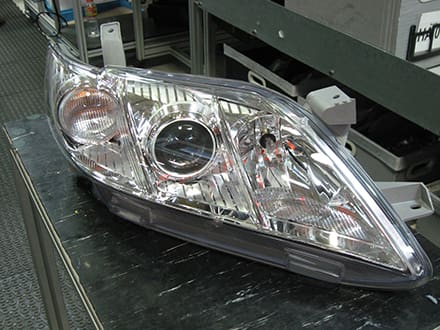