Custom Wire Tech Partners with K-Kolor for Mission Critical Printing on Custom Medical Devices
Custom Wire Technologies of Port Washington, Wisconsin offers contract manufacturing of custom wire products with capabilities for wire diameter sizes as small as .001″. Their products are used in the medical field and require mission critical performance.
As an ISO 9001 certified operation, the company continually searches for ways to improve the quality of their products. In some cases, this leads them to take greater control of value adding operations.
The Custom Wire Technologies facility features custom pieces of integrated manufacturing equipment specifically optimized for the production of custom wire products with excruciatingly tight tolerance specifications.
In-house Printing
Until recently, the company outsourced printing on their manufactured products. Seeing an opportunity to expedite manufacturing times by taking control of print operations, President Bob Boldig developed a partnership with Wisconsin-based K-Kolor.
K-Kolor provides expertise with inkjet and pad printing on a wide variety of materials. When they found ink would not bond to a product made from LLDPE, they consulted with their pad printing manufacturer which recommended a Marabu ink along with an Enercon surface treater.
K-Kolor President Ron Kohl says, “Enercon provided several rounds of complimentary lab testing to help us qualify the process.” The trials proved that the blown-arc air plasma surface treater makes the printing indelible. Kohl adds, “For medical printing applications it’s imperative to follow the defined protocols. Enercon’s experience with medical device applications ensured the project went very smoothly.”
To automate the treatment process, Boldig’s team designed an integrated robotic feeding system that precisely positions and rotates the wire products in the treatment zone. Printing is achieved with the pad printer, which utilizes a rotary fixture for rotational printing. Since partnering with K-Kolor, Custom Wire Technologies increased its printing throughput and reduced the number of pieces rejected due to printing imperfections.
Other Applications
The power of surface treating has made an impression on Boldig. “I’m really impressed with the improvement in adhesion these compact systems provide. In fact, we tested the system for a few other applications in our facility.”
One of the other adhesion improving applications involved an experimental fixture the company was developing with a bottle and industrial grade velcro. “We used cleaning solvents on the bottle and we still could not get the industrial grade velcro to hold the bottle in place.” Boldig decided to pass the bottle through the treatment zone of the blown-arc plasma treater to see if adhesion would improve. The results were impressive.
“The bond created between the adhesive on the velcro backing and the bottle was so strong that it held up while the bond between the velcro and the backing itself failed. As a manufacturer, a surface treater is a great tool to have in your facility,” says Boldig.
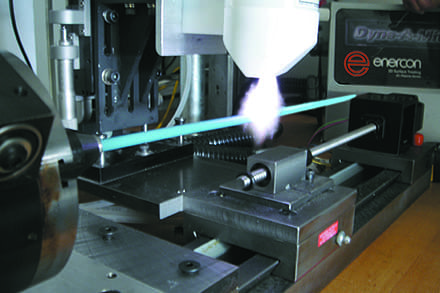