Surface Modification Techniques For Optimizing Adhesion To Automotive Plastics
Automotive plastics with a low polarity, such as PE, PP, TPO, POM, PUR and PTFE typically require surface treatment when decoration is required. Metallic surfaces may also require cleaning to remove low molecular weight organic materials prior to decoration. Once the above-mentioned interior and exterior grades of substrate surfaces are cleaned and activated, printing, gluing and painting are possible without the use of adhesion-promoting primers. This paper describes the latest innovations in three-dimensional surface treating technology for plastics finishing which address the need to advance adhesion properties, increase product quality, and achieve environmental objectives within the automotive industry. These innovations include advanced thermal and non-thermal discharge treatment processes for raising the polarity of surfaces to be painted, bonded, decorated, laminated, printed or to have tape applied.
The utilization of plastics in the production of automotive parts has been steadily growing worldwide. Considering their key functional advantages, plastics have good performance characteristics, are
lightweight, relatively inexpensive and are easy to manufacture. Among the various types of plastic
which are used in automotive parts, thermoplastic polyolefins (TPO) have become the material of
choice for exterior automotive applications such as bumpers and claddings. TPO and PP are the fastest
growing due to their mechanical properties and their advantages relative to recycling.
Download this informative technical paper.
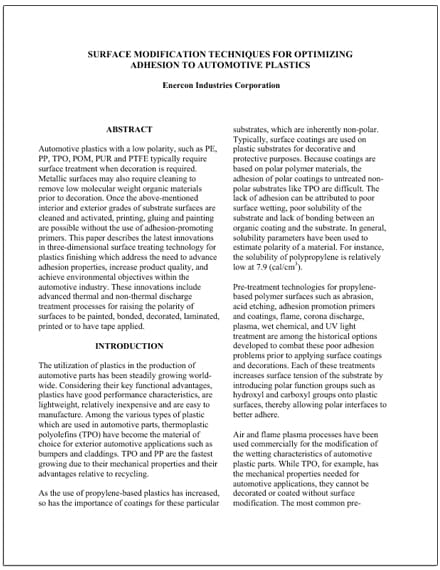