Plasma & Flame Treatment Prepares Aluminum Surfaces for Bonding
Bonding to aluminum can be major challenge. Engineers typically rely on adhesives to bond aluminum without welding. Depending upon application requirements, there are several adhesives and VHB foam tapes that have proven effective. However, all adhesive-based remedies are subject to failure if surface preparation is overlooked.
Aluminum Surface Contaminates
Aluminum is often annealed to achieve high speed processing properties, surface wettability, adhesion and chemical resistance. While the annealed aluminum is still pliable it goes through the rolling process. It is sprayed with oils containing alcohols and esters to help increase the rolling process life and reduce mill power consumption. During this procedure the oils can become contaminated with other oils and hydraulic fluids, impairing adhesion.
Another contaminate that can occur on the surface is an amorphous oxide layer that is formed as a result of a chemical reaction between oxygen and humidity in the air after rolling. During the annealing process, this oxide forms the barrier which grows thicker as a result of both the increased diffusion of oxygen through the oxide layer and the chemical reaction of the aluminum under heat. The heat of annealing promotes water loss and a more compact oxide, essentially creating a barrier layer on top of the aluminum.
Aluminum surfaces will vary considerably because of variations in oil and oxide contamination concentrations. In addition, the annealing of aluminum coils creates a big difference from the outside edge to inside core of the coil roll because air (O2 and H2O) is present at the edges. So there’s a thicker oxide layer at the edges as opposed to the middle of the coil.
How do you level the playing field so adhesion across aluminum surfaces can be uniform and predicable?
Dry surface treating techniques clean the surface of the rolling oil deposits and break down oxides. Surface modification can be accomplished using corona (air plasma), flame, atmospheric plasma treatment systems, or combinations of these approaches.
The use of these surface treating systems can also improve aluminum grain definition, contribute to achieving a specified chemically functionalization, and promote mechanical/chemical bond strength. Users can save time and production costs by eliminating the use of off-line wet chemical surfactants which require effluent waste disposal.
The level of corona, flame or plasma treatment improves surface adhesion, usually at <5° contact angle, which can assure consistent adhesive adhesion results relative to MIL specs. More interfacial surface energy can be created to a level defined by “watt density”.
Composite use on the rise
More and more composite structures are being developed to replace their heavier aluminum counterparts. The good news is that plasma and flame surface treaters are also effective in increasing their wettability with adhesives, inks and other coatings.
If you have bonding issues with aluminum or composites, you should consider in-line surface preparation. We recommend taking advantage of Enercon’s complimentary lab trials to evaluate whether corona, flame or plasma treatment properly prepare your aluminum application for bonding success.
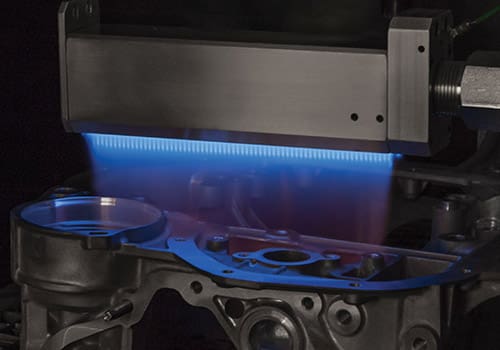