Automotive Parts Supplier Eliminates Hazardous Adhesion Promoter with Enercon Plasma Treating Technology – Saves $850,000, Improves Productivity & Quality while creating a Safer Work Environment.
The integration of an Enercon plasma surface treater into Champion Plastics (Auburn Hills, MI USA) operations will save the company $850,000 on a multi-year project they have with General Motors.
The company supplies an injection molded TPV (thermoplastic vulcanizate) seal for a gap in the spoiler of a GM vehicle to improve fuel economy. After molding, the part requires the application of a double-sided tape. Like many plastics, TPV has a very inert surface. Its low surface energy makes it difficult for adhesives to successfully bond with the surface.
To enable bonding with the TPV, Champion Plastics’ employees would manually prep the surface by applying a liquid adhesion promoter prior to adhering the double-sided tape. To ensure their safety, employees would follow special handling guidelines. The manual production process of applying the liquid adhesion promoter was very labor intensive and subject to human error which impacted quality. Champion Plastics looked for options to improve their work environment, increase productivity, and save money by repurposing labor to other value adding operations.
The company decided to invest in an Enercon Blown-ion™ atmospheric plasma treater. The system produces a powerful, yet gentle plasma that cleans, etches and functionalizes surfaces by bombarding them with an intense, high-speed discharge of ions. This increases the surface energy and wettability of the TPV enabling bonding with the double-sided tape.
Champion Plastics mechanically and electrically integrated the plasma treating technology into their blow molding operations as part of an automated production process. This automated process improved their productivity, ensured consistent quality, eliminated the hazardous primer, and allowed them to repurpose their workforce on higher value operations.
Champion Plastics was recognized for their efforts by winning an Innovation Award from the Manufacturers Association of Plastics Processors.
A video of the system in operation and interview with Champion Plastics President Jeff Ignatowski is available here.
Enercon’s in-line plasma and flame surface treating technologies are used in manufacturing, assembly & decorating operations to improve adhesion of inks, adhesives and coatings. The technologies may be integrated with robotics, conveyors and indexing machines to improve product quality and throughput.
Companies in the automotive, battery, packaging, consumer products, medical, window & door, wire & cable, assembly, printing, and decorating markets rely on Enercon surface treating technologies for repeatable results.
More info about this story can be found in our webinar library.
Release date: 8/11/2023
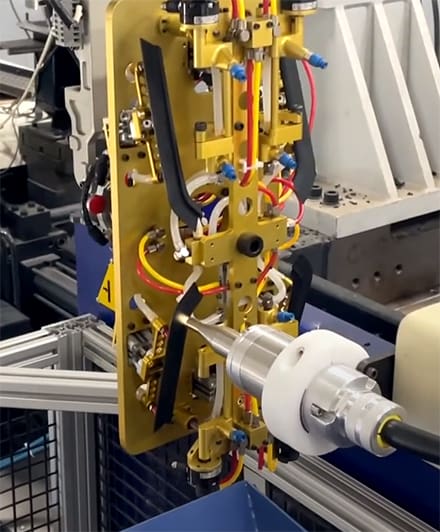