Three Mistakes to Avoid When Plasma Treating
We have many customers who have tried a corona or plasma treating solution in the past with failed results and were very hesitant to give plasma a second try. However, there are three areas which can be corrected for improved results: using the right plasma technology with the proper set up, having the proper protocols for determining success, and ensuring proper handling and testing of treated samples. Let’s take a look at each of these situations.
1. Thinking that all plasma is the same.
Lab trials prove blown arc, blown ion, variable chemistry plasma and flame can produce remarkably different results. Each of these plasma technologies have unique properties which can be the difference between success and failure. Additionally, the proper application of each technology relative to dwell time, optimizing treatment distance, and the time between treatment and additional processing are critical for success. All of these variables can impact the success of treatment.
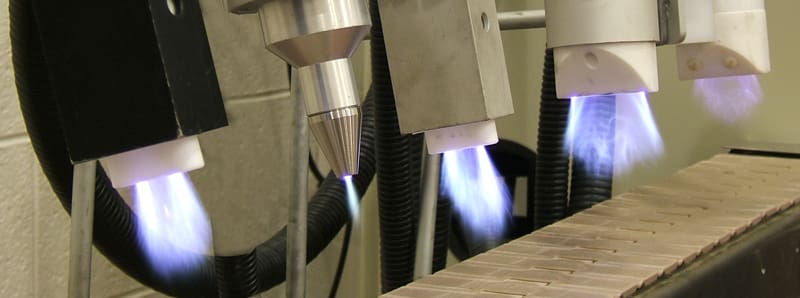
2. Leaning too heavily or too lightly on a single indicator of treatment success.
Many operations are looking for a target dyne level. While dyne level is a valuable indicator of a change in surface energy, dyne level does not guarantee adhesion. In some cases, we have seen minimal or no change in dyne level — yet, the adhesion of an ink or adhesive improves. More advanced surface analysis techniques, including contact angle measurement and measuring of polar groups on a surface, can provide more insights on changes to a surface after treating.
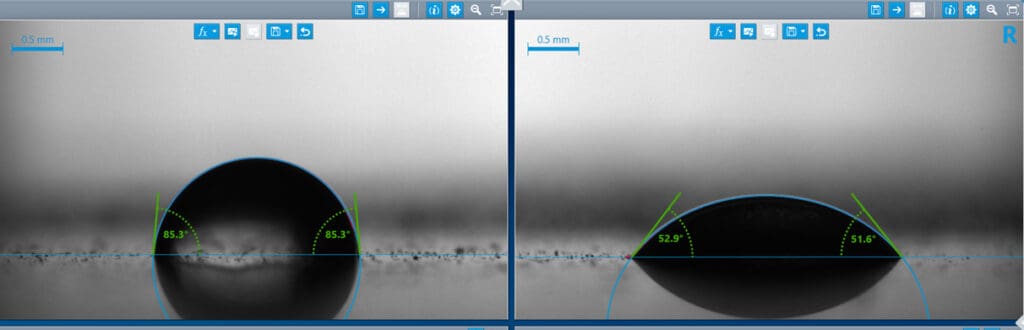
However, the ultimate test is running a treated surface through your process and measuring the success of the treatment based on your tests for acceptable adhesion.
3. Mishandling or mistiming the testing of treated samples.
As a free service to our customers, Enercon provides laboratory testing with multiple treatment technologies. In many cases, we ship the treated parts back to the customer with overnight delivery to additional testing and evaluation. There are two potential pitfalls to be aware of when handling parts in this situation. The first pitfall is making sure that everyone on your team is aware of the sensitivity of the treated surface. Handling the parts could leave oils from your skin or leaving it out in a ship environment could lead to surface contamination and negatively affect the benefits for the treatment.
The second pitfall that can occur is waiting too long to run secondary testing. All materials will respond differently to treatment and will show inherently different decay rates of the treatment. It is not uncommon for a treated surface to lose some of its peak dyne level after hours or days of being treated.
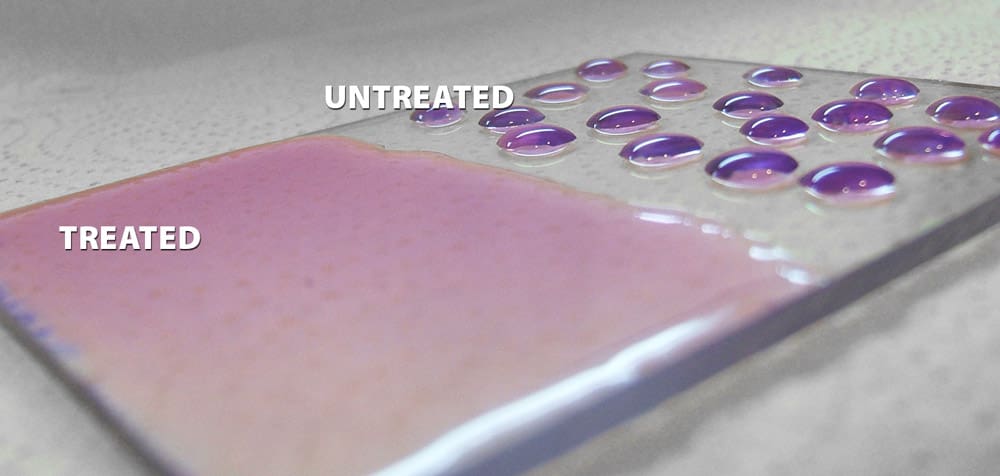
Meanwhile, some materials will hold treatment levels for extended periods of time. It’s important to understand this variable and that is why Enercon always recommends installing a plasma treater in a spot that reduces the time between treatment and the next part of your process.
Please consult with Enercon’s Application Experts if you have any questions on promoting adhesion. In addition to free expert consultation we also offer the services of our laboratory where we can put your application to the test.