Plasma Treatment Improves Print Durability on Nexans’ Wire
Nexans is the one of the largest wire and cable manufacturers in the world. Their corporate headquarters in France directs 26,000 employees in over 40 countries in serving a wide range of industries ranging from transportation to communication, from aerospace to residential. As a global expert in wire and cable, Nexans is committed to developing innovative products and processes that meet their customer needs.
Nexans’ Fergus, Ontario plant in Canada specializes in manufacturing electrical wire for residential buildings and utility control cable applications. Their products are available through distributors, as well as big box home improvement retailers such as Canada’s Rona. The facility transforms polyethylene resin and raw copper and aluminum rods into insulated wire ready for your next DIY project.
Poor Print Durability Sparks Experiments on Surface Adhesion
Hal Armstrong, Quality Assurance and Process Engineer Manager, is at the forefront of ensuring Nexans’ products are aligned with their corporate vision. He ensures their products meet all industrial regulations and customer standards. His team is also responsible for evaluating and implementing new technology and processes to improve quality and efficiencies.
One challenge that his team spent years trying to resolve was improving inkjet print durability on their polyethylene jacketed wire. Customers complained that the text, or legend, on the wire would rub off during installation. In fact, even before leaving Nexans facility their quality control team would detect ink rubbing off when winding on a reel or during the cabling process. Print adhesion quality is not only important for customer satisfaction, but it is also critical for compliance with Canadian Standards Association (CSA) and Underwriters Laboratories (UL).
“When the ink didn’t stick, it caused us a significant amount of rework. We had to reprint all the wire,” explains Armstrong. His team experimented with several methods to remedy the problem such as: hot air guns, open flame, numerous quick dry inks and a static eliminator.
After consulting with their raw material supplier, Dow, the team began to focus on the surface energy incompatibility between the polyethylene surface and the ink. Polyethylene in its native form is non-porous and hydrophobic. It has low surface energy due to low levels of charged ions on the surface. Additionally, any type of surface contamination negatively affects adhesion. Contamination can include material additives and release agents which can migrate to the surface during extrusion.
Discovery of Plasma Creates Positive Bond
Armstrong discovered Enercon’s in-line plasma treating systems in 2012 at the Interwire tradeshow. His team consigned an Enercon Blown Ion Series plasma treater from Enercon’s local representative in Ontario, WebConvert.
Blown ion plasma generates a concentrated discharge that bombards the material’s surface with a high-speed discharge of ions. The positive ion bombardment removes contaminates and raises the surface energy of polyethylene by cleaning, etching and functionalizing the surface. The plasma treated surfaces provided instant results.
“Our operators could see an immediate improvement in print quality,” says Armstrong. “We applied UL/CSA Spec.2556 Durability of Ink Printing method to measure the success. It involves using a weighted apparatus that rubs the wire back and forth to test the durability of the ink adhesion. Prior to applying the plasma treatment the ink would rub off after one and a half cycles, now we can get over ten cycles. That far exceeds CSA’s requirement.”
The plasma treater integrated seamlessly into Nexans’ line. The treatment head is mounted directly after the extruded Poly is applied to the wire, and prior to their Markem-Imaje inkjet printer. After printing, the wire is immersed in a water bath to cool down the jacketing before it is wound onto a reel. Nexans also integrated the plasma treater’s power control into their PLC so that the treater will automatically turn off when the extrusion line is shut down.
“The Enercon plasma treater is easy to use and reliable. You just push a button and ‘boom’, you’re running. Our plasma treater is running constantly and we have not had to do any maintenance or replace a single part.” says Armstrong.
Over the course of two years Nexans purchased a total of three Enercon blown ion plasma treaters. The success snowballed from there. Additional Nexans plants located throughout North America learned of the results from surface treatment and have adapted their process to include Enercon’s blown ion plasma treater.
True to their corporate philosophy, Nexans relentlessly explored methods to improve their printing process to satisfy their customer’s need. Since integrating a plasma treater, customer complaints about printing have been eliminated. In addition, to improving quality, Nexans has also increased their overall productivity by eliminating the time and scrap associated with reprinting.
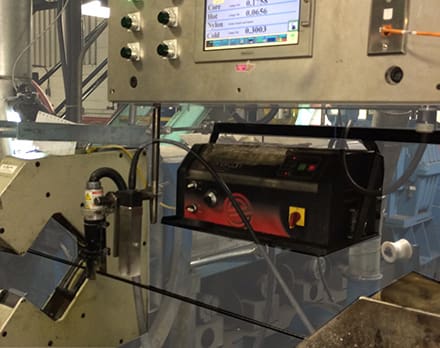