Using Dyne Solutions and Dyne Pens to Measure Surface Energy On Non-Porous Substrates
Non-porous substrates, such as polyethylene, polypropylene and foils, need to have their surface energies altered in order for the proper flexographic ink adhesion to occur. An old general rule of thumb is that the substrate should have a dyne level (surface-energy measurement) of at least 10 dynes higher than the surface energy of the ink applied to the surface. This can be used as a starting point, but consult with your suppliers & test your processes for your optimal target.
The generally accepted solution to verify dyne levels or surface energy is a mixture of Ethyl Cellosolve and Formamide. This solution contains a dye to make it easier to see. When using these wetting tension solutions, all safety precautions as listed on the labels should be observed, as there are specific hazards associated with using them. These solutions also have a shelf life of only around six months, so they should be properly dated at time of use and replaced when the expiration date has been reached. If this isn’t done, false dyne information could result, along with a rejection of printed material by the customer.
There are also water-based dyne solutions and pens available which can also be used to measure surface energy. Whichever you choose to use make sure to follow the manufacturer’s instructions for properly conducting your test.
There are three methods that are generally used to check the surface energy of a substrate using Ethyl Cellosolve and Formamide. They are the cotton-swab applicator method, the dyne-pen method, and the drawdown test method.
Cotton swab applicator method
Dyne solutions of various concentrations are placed on the substrate until a solution is found that only wets the surface of the film. The tip of the applicator is immersed in the test solution from a calibrated dyne-level solution stock container. The solution is spread lightly over approximately one square inch of the test material. If the wetting solution stays intact for two seconds the treat level is at least as high as the dyne level recorded on the bottle of solution. Repeat the procedure until a solution is used that beads up on the surface of the material being used. The film treat level would then be identified as the last solution tested that remains wetted out on the surface. A clean cotton applicator must be used for each test repeated to avoid contamination of the different solutions and possible distortion of results.
This method has been a standard for years but is still somewhat subjective and inconsistent because of the personnel involved in the application of the fluid to the substrate. This procedure should be done in a lab environment because there is always a risk of spilling the contents of the bottles or leaving the used swabs lying around that could lead to skin contact.
The dyne-pen method
This is a press-side method that is usually used by the operator to check the treat level of a substrate just prior to print. Pens with built-in applicators resembling felt-tip markers are pulled across the entire web in a straight line. The pens have the dyne level of that pen listed on them. As the pen is drawn across the web the operator looks to see that the solid line does not break up over the recommended time prescribed by the pen supplier.
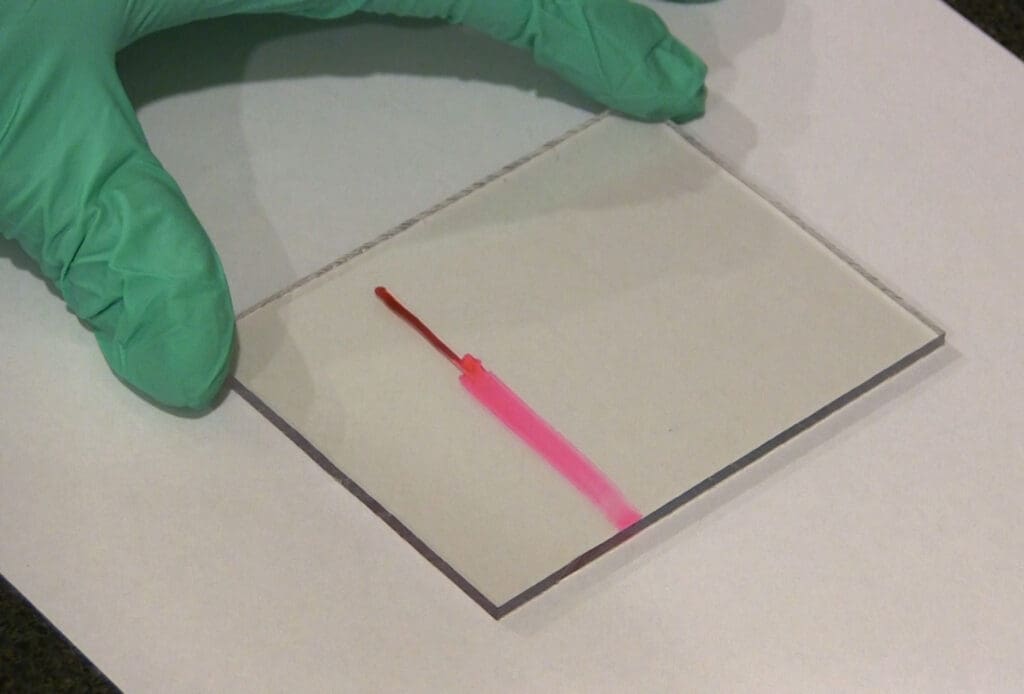
This method is not highly accurate because of possible contamination of the tip by multiple use. The advantages are that it is a quick method, also shows the operator which side is treated, and checks for the condition known as back-treat. These pens must be dated when first used, the tip sealed immediately after use, and the pens thrown away when the six-month expiration dates have been reached.
The draw-down test method
This is the most accurate of the surface-energy measurement systems. A substrate sample, usually measuring 81/2 x 11 inches, is clamped to a clipboard. At the top, a drop of three different dyne solutions that bracket the desired treatment level are placed horizontally from each other. A wire wrapped metering rod is then placed just above the droplets and pulled down. When a film of liquid breaks within the two-second period the tester knows that the treat level of the film is below what is written on the dyne solution bottle. This test tends to be more accurate because the metering rod lays the solutions down at the same relative thickness. The rod must be thoroughly cleaned after each use.
The testing of a film’s surface energy prior to printing is a necessary task, and helps to eliminate another of the many print variables of flexo. Testing also insures a material that will be acceptable to the print buyer.
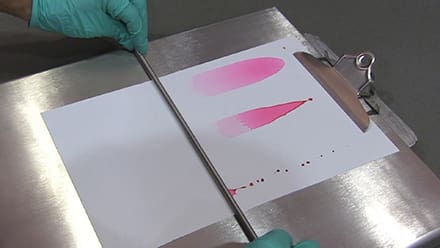