Roll Aluminum Surface Preparation for Packaging Applications
The packaging industries within North America and Western Europe consume the majority of the aluminum sheet and foil for making beverage cans, flexible packaging and foil wraps. The choice of alloy for these applications typically predetermines properties such as strength, formability and resistance to corrosion. Other requirements such as the surface finish, flatness and gauge uniformity of aluminum are achieved through careful attention to the mechanics and chemistry of the rolling process. A knowledge of the influence of the starting stock surface condition, surface condition of the oils and lubrication used, along with an understanding of the effect of roll coatings, tension levelers and other coil management related variables is key.
In order to improve surface properties of those products manufactured of aluminum and not directly related to packaging such as wear resistance, corrosion resistance, reflectivity etc., different types of surface treatment have been designed and integrated into manufacturing operations. These are typically categorized into several groups, such as electrochemical treatments, chemical treatments and coatings. The state-of-the-art chemical surface treatments, for instance, for bonding of aluminum and aluminum alloys with adhesives such as phosphoric acid anodizing (PAA) are the basis for present high-strength and durable adhesive bonds. Because of increasingly strict regulations on the use of wet chemicals, this discussion will focus on the surface characteristics of aluminum and the discharge surface treatment technologies which can effectively clean and functionalize those surfaces.
Aluminum Surface Characteristics
The surface characteristics of aluminum are critically important in achieving good wettability, bond formation, and durable adhesion on this substrate. In the form of a coil, most hard aluminum foil undergoes annealing to re-crystallize the grain structure and remove the rolling oil. In addition to these tasks, the main purpose of annealing is to generate a surface that has even wettability with high chemical resistance and provides consistent adhesion properties. Also, maintaining good unwinding behavior especially for thin foil is essential to avoid uncontrolled oxide growth that can lead to the foil sticking together during unwinding. After rolling, a continuous amorphous oxide layer forms immediately due to the reaction between oxygen and humidity from the environment and the freshly generated metal surface. During annealing at temperatures of approximately 300°C, this oxide grows thicker due to elevated diffusion of oxygen through the oxide and reactivity with the metal in the oven atmosphere. The oxide growth occurs at the interface between oxide and metal. The oxide on top changes during annealing, accompanied by a loss of water leading to a more compact oxide of generally higher resistance. Also, after annealing, rolling oil residue layer concentrations tend to form at higher levels within the middle of rolls than at the edges.
Although extremely high wettability is not really necessary for good surface adhesion, a defined degree of surface cleaning and functionalization will significantly enhance ink, coating and polymer adhesion for structures. One such structure is the stand-up pouch which usually uses a two-component polyester-polyurethane laminating adhesive. Since oxide growth can lead to adhesion failure, surface treatment systems such as corona, flame or atmospheric plasma can reduce oxide levels and polarize the surface to increase adhesion.
Surface Cleaning / Functionalizing Methods
Among the discharge surface treatment technologies available to be used in the cleaning and pretreatment of aluminum coils, the processes of corona, flame and atmospheric plasma all contribute effective and relative degrees of surface cleaning, etching and functionalization for the promotion of adhesion to polymers.
Air plasma, or corona discharge, is filamentary in affect and at high power densities will remove approximately 10mg/m² of rolling oils from the surface at production speeds without an optically recognizable modification at the aluminum surface. The efficiency of this treatment method depends on the level of surface contamination present since the filamentary discharge is not homogenous across the treatment area.
Atmospheric (chemical) plasma is a non-thermal treatment process which provides the advantage of creating a non-filamentary discharge with homogenous reactive etching, cleaning and functionalization (including oxidation) at the surface of aluminum and the aggregation of particles by the activated atoms, radicals and metastable species in the plasma space. Atmospheric plasma glow discharge is a high-density plasma capable of removing up to approximately 55 mg/m² of residual surface oil at production speeds without an optically recognizable modification at the aluminum surface.
Flame plasma surface treatment is similar in homogeneity to atmospheric plasma insofar as the species contained in the flame plasma are highly reactive and affect electron distribution and polarity at the surface of aluminum. As a thermal discharge, the reactive by-products are primarily carbon dioxide, water vapor and heat. Flame plasma pretreatment slightly modifies aluminum surface chemistry, typically leading to a contact angle of less than 60°, increases the oxygen content ratio, and drastically improved bond strength. Flame plasma is most suited for cleaning surface contaminations in excess of 55 mg/m².
Relative to extrusion coating and polymer film lamination adhesion on aluminum, the degree of surface pre-treatment oxidation affected to the adhering polymer is primarily responsible for adhesion. The dwell time in the air gap, the temperature of the substrate, the pre-treatment technology, and the characteristics of the polymer material all have an influence. Air plasma and ozone provide the most oxidative effect to extrudates. Functional groups deposited on polymer films by atmospheric chemical plasma offer the opportunity to vary the chemical group interface. Both atmospheric chemical plasma and flame plasma more homogeneously treat the adhering side of the film.
Technology Application
The selection of appropriate tie-resins and adhesives are, alone, not sufficient to achieve and ensure effective and robust surface adhesion. Because the surface of aluminum acts as a barrier in a laminate, absorbents or migrating matter such as moisture or additives for machine processing for plastic films can have an influence on adhesion. They can accumulate in front of the barrier or can react at the interface where these additives are present at elevated temperature. Adhesion failure occurs as a result of the replacement or the infiltration of interfacial bonds. All foil applications require particular attention to the proper functional barrier in the plastic coating or film lamination when initially designing the laminate.
The removal of migrating additives on plastic film surfaces, the increase in surface energy, and the deposition of surface functionalities will optimize the plastic surface interface for adhesion. Just as critical for complete adhesion is the removal of aluminum surface contaminations such as residual rolling oils. Use of an atmospheric plasma or flame plasma discharge technology can cost-effectively bombard these surfaces with electrons and ions, displace surface contaminants, and add chemical functionalities to promote covalent bonding at the interface with extruded polymers and laminating films.
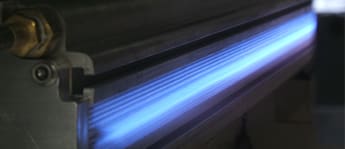