Improving UV Coating Results with Corona & Plasma Surface Preparation
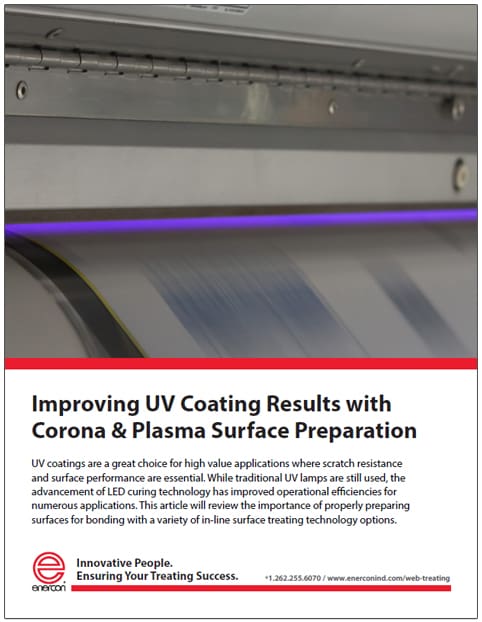
UV coatings are a great choice for high value applications where scratch resistance and surface performance are essential. While traditional UV lamps are still used, the advancement of LED curing technology has improved operational efficiencies for numerous applications.
As seen in the UV+EB Technology Magazine, this article reviews the importance of properly preparing surfaces for bonding with a variety of in-line surface treating technology options.