Troubleshooting Surface Treating for Flexographic Printing Process
Want to learn more about your flexographic printing process? Want your operators to have more control over the press? Then learn the power of asking “why”.
Three letters that add up to a powerful and revealing question. When we were three and four years old, it was our favorite question. It often stymied Mom and Dad, and it was the way we learned how things in the world worked. Unfortunately, as we get older, we tend to let other pressures squash our inquisitive human nature and we fail to ask this powerful question.
Think of your own converting or extruding line. How many of your line personnel know “why” they do things a certain way? Is it because that’s the way “old Joe” the supervisor told them to do it? Is it “because…because… well, it just works, that’s why.”
If your team isn’t asking and learning “why”, then it may be time for some continuing education.
The Real-World Importance of “Why”
Think about the differences in the materials you print on from only 5 years ago. How many fractional gauge substrates were you handling? How many multi-laminates were you running? New substrates and specialty ink formulations have shrunk the operating window that your operators have to work with.
This makes it more important than ever for your line operators to understand the flexographic printing process. Your suppliers are a good place to start and you should demand as much information as possible from them. Your ink manufacturer can tell you how their ink is intended to be used, but they can’t tell you how to successfully print. The press manufacturer can tell you how the press operates, but they can’t teach you how to print.
Understand that press and ink manufacturers supply the tools and that the printing process is in your hands. The better you are at it, the more profitable you become.
Printing or treating?
The power of understanding your process and asking “why” also benefits you when it comes to troubleshooting. Take for example a situation where you notice ink picking after winding. If your team understands the corona treatment process, then they can immediately perform some tests to see if the treater or treat level is the cause.
If the problem is occurring in only one spot, you might suspect backside treatment. Backside treatment occurs when air is entrapped between the backside of the web and the ground roll. The air beneath the web becomes ionized & corona treatment occurs.
The cause of backside treatment can be attributed to either material imperfections or operational problems. Wrinkles in film, scalloped edges or “bagging” are all material conditions that promote backside treatment.
A simple dyne test can tell you if you have backside treatment. For more information on eliminating backside treatment, contact us for an article on backside treatment.
Once you’ve determined that backside treatment isn’t the cause of ink picking, you can turn your attention to other potential causes. Ink formulations, drying time and winding tension may be to blame.
Where can you go to learn more?
I recently spoke with Technical Flexographic Instructor Steve Utschig of Fox Valley Technical College. He affirmed that the Flexographic printing process is fairly simple and very predictable. However, as humans sometimes do, we tend to “mess it up.”
In his experience, Steve says he would estimate that 50% of all flexo problems result from mishandling ink. Another 30% result from poor make readies and improper set-up and about 20% are mechanical.
Educational programs like the ones Steve conducts at Fox Valley go a long way in reducing the human errors that reduce your profits. They preach a vigilance to documenting your own procedures and encouraging your team to always ask “Why?”.
If you have some topics on surface treating that you want to learn more about, contact Enercon.
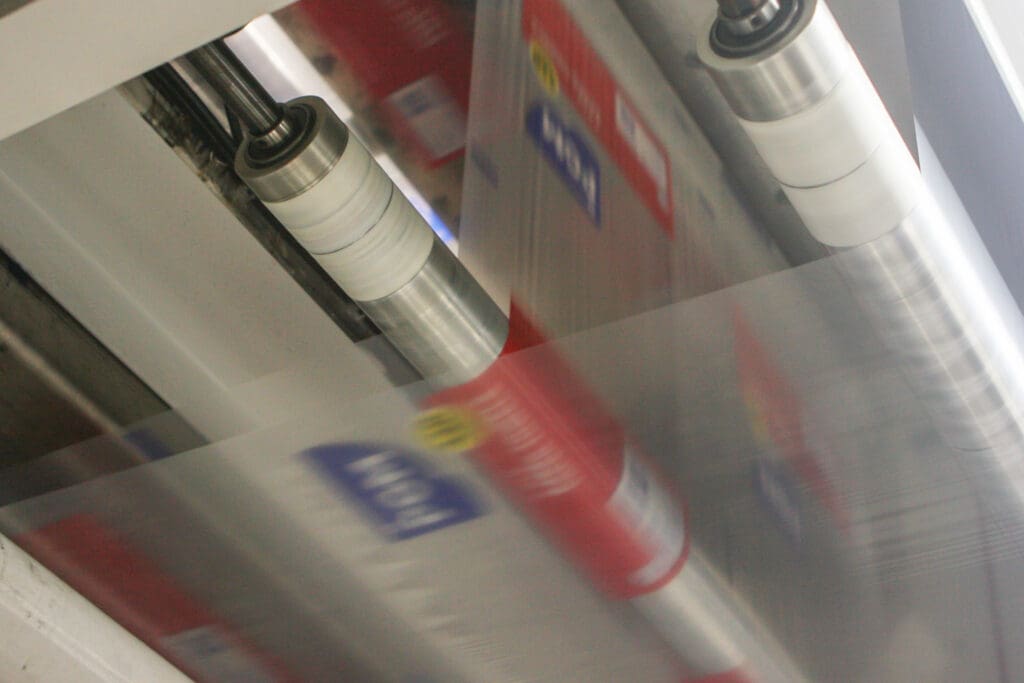