Troubleshooting Dyne Levels for Cast and Blown Film Lines
“That film you sent me was supposed to be 42 dynes! I can’t convert this stuff and I’ve got orders due!!!” exclaims the exasperated converter. “Hold on a minute, I’m sure we shipped you film that was 42 dynes, let me look into this,” contends the film producer. When dyne levels are insufficient, it’s a problem for everyone. And in most cases, finding the cause(s) is a bit more complicated than pointing fingers.
Blame the corona treater
Since the corona treater is responsible for raising dyne levels, many operations will jump to the conclusion that there must be something wrong with the treater. Fortunately, it’s pretty easy to tell if there is a problem with the corona treater. But before we look at the corona treater, let’s think about the specific problem.
In our example, the film producer says their records show that they shipped film with a dyne level of 42. If that’s true, then there are only a few possibilities:
- inaccurate dyne testing
- process inconsistency
- post shipment changes
Inaccurate dyne testing
Enercon has long supported the ASTM guidelines for Meyer rod draw down testing with dyne solutions. However, we recognize it is often more practical to conduct quick pass/fail tests with dyne pens.
In either case, there is a subjective and interpretive nature to these tests which can vary results several dynes, based on the person doing the testing. It is important to have consistent procedures in place to ensure accurate testing.
Process Inconsistency
Inconsistencies on the film line will create inconsistent treatment results. Consider that the treater is set-up to generate a specific watt density for the film and line speed be processed. What are the variables that can affect the treatment results?
If you have a proven application recipe (say a 1.5 watt density at 250 mpm producing a dyne level of 42 dynes) and you are getting a different dyne level result, the first thing to examine is changes in the resin. Have you recently changed resin suppliers? Has an additive been added or removed? These factors can affect your treatment results.
A less obvious cause can be variances in the temperature of the chill roll and its position relative to the treater. Warm film demonstrates a greater responsiveness to corona treatment. If the chill roll temperature is not properly maintained, treatment results can vary.
Post-shipment changes
Changes in dyne level over time are common. If film has been inventoried for a long period of time or exposed to environmental conditions, dyne level from corona treatment will decay. Another cause of dyne level decay are additives rising to the surface. This can cause problems for the converter.
Why smart converters bump treat
With so many variables at play, it’s no wonder that smart converters bump treat material as part of their converting operation. This provides them with the added insurance that the dyne levels are optimized for their specific process.
The added control of in-line bump treating allows converters to respond to any dyne level issues on the spot. Think about it, instead of worrying about who to blame while your line is down, you can actually be running production!
What about the corona treater?
In the beginning of this article, I mentioned that it is easy to determine if the corona treater is causing a problem with dyne levels. The most common problems are an improperly set watt density, an inconsistent electrode air gap, or an interlock failure that has turned the treater off.
There’s little doubt troubleshooting dyne levels issues can be tricky, but with a better understanding of your process variables and a little help from bump treating, converters’ dyne level problems’ will be a thing of the past.
If you are have a question about troubleshooting your application or bump treating, fill out the form to the right and our application expert will contact you.
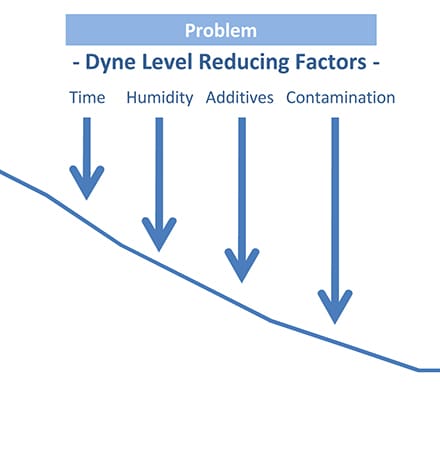