Solving Metallized Film Converting Adhesion Issues
Most application questions involving the converting of metallized films concern the dyne level required to convert. It is extremely important for both the film manufacturer and the converter to recognize that achieving a specific dyne level does not guarantee printing, coating or laminating adhesion.
Most converters will conduct a dyne test on metallized film prior to converting. While this is good practice, converters should be aware that dyne level measures wettability not adhesion. Dyne levels can be used to help predict the chances of adhesion success, but there are numerous material and process variables which can significantly effect adhesion success. Additionally it is important to note that consistent dyne level testing accuracy is subject to individual subjectivity and other environmental challenges.
Key considerations when relying on dyne levels to predict adhesion success:
- Dyne level tests are highly dependent on the individual conducting the test.
- is the test conducted correctly and consistently each time?
- is testing conducted in a manner that accounts for environmental variables such as temperature, humidity, age of dyne solutions, cleanliness of swabs/pens and material?
- are the results interpreted consistently? (it is not uncommon for two experienced individuals to report a variation of several dynes on the same substrate)
- It is impossible to guarantee a dyne level reading is representative of the entire roll.
- was the entire roll of material treated with exactly the same watt density, at precisely the same air gap and controlled temperature as the area tested?
- Dyne levels decay over time.
- additives used to make film easy to handle rise to the surface over time creating lower surface energy.
- in addition to time, storage conditions of the material can impact the longevity of dyne levels, this includes cross contamination from the back side of rolled material.
- Dyne levels measure wettability, not adhesion.
- recommended dyne levels for converting are provided by ink, coating and adhesive suppliers. It is not uncommon to have successful adhesion with lesser dyne levels.
- changes in material suppliers or film ingredients and changes in process variables such as line speeds and ink/adhesive/coating formulations can significantly affect bonding and alter the desired dyne level.
To summarize:
- Dyne level readings have inherent challenges which lead to variations in measurements
- Dyne levels do not guarantee adhesion
- Dyne levels decay over time
- Dyne level decay is accelerated by environment
- Dyne level decay is accelerated by slip aliitives rising up to the film surface
- Dyne levels can be contaminated from the underside of the film when rolled
So what’s a converter to do?
Both the metallized film supplier and converter are at the mercy of the physics involved with dyne levels. Controlled storage facilities and a timely inventory procedures certainly help, but with all these variables at play its clear that a metallized film supplier can not reliably provide convertible material 100% of the time.
The industry’s best practice is to eliminate dyne level decay issues by bump corona treating the material at the time of converting to create a fresh clean surface ready for bonding. This puts the converter in control of the substrate surface energy and his value added process.
We invite you to download this entire technical article in PDF format to access additional information from independent industry experts who provide their opinions on converting metallized films.
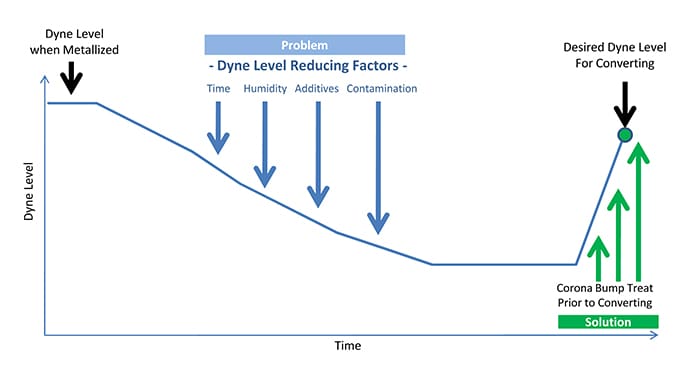