Prevent Backside Treatment
The bad news is that backside treatment mitigates the effects of surface treating. In some cases, it results in under treatment of substrates.
It can also raise the energy of the backside surface creating processing problems. In bag making and seal applications, backside treatment can alter the substrate’s co-efficient of friction. This will ultimately cause problems in converting the material downstream.
The good news is that backside treatment is easy to understand and prevent.
The first thing to recognize about backside treatment is that it is a potential problem for both bare and covered roll treating systems. It occurs when air is entrapped between the backside of the web and the ground roll. The air beneath the web becomes ionized & corona treatment occurs.
Material Imperfections
The cause of backside treatment can be attributed to either material imperfections or operational problems. Wrinkles in film, scalloped edges or “bagging” are all material conditions that promote backside treatment.
By examining the results of simple surface energy measurements, you can often identify the probable cause of backside treatment.
Figure 1 shows the unique pattern of surface energy resulting from a wrinkled web.
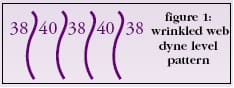
Figure 2 shows a “blob” pattern that is often caused by a “bagging” condition on the center or edge of the web.
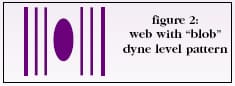
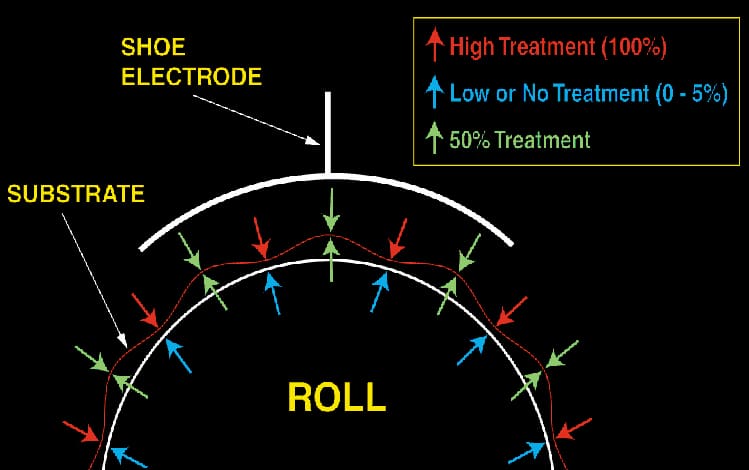
Backside treatment not only results in treatment of the back of the substrate, it also causes undertreatment of the front side
System Issues
Backside treatment may also be related to system conditions including web tension and system cleanliness. To troubleshoot these problems, first check to ensure the web is threaded properly. Next, check web tension and be sure the substrate is flattened on the ground roll. It is imperative that the substrate travels across the ground roll surface smoothly and at proper tension to avoid potential air pockets.
If proper tension cannot be maintained consider employing a nip roll and treater roll drive. In fact if you’re running at high speeds, in excess of 700 ft/minute you should have a nip roll and a drive.
If these solutions do not remedy the backside treatment, then reduce the speed of the application. This will reduce the effect of the laminar airflow that travels across the web.
If you’re operating a covered roll system, you should examine your roll covering and look for any nicks, gouges or debris on the surface. These should be either patched or cleaned, or the roll should be replaced.
Common causes of backside treatment:
- Material imperfections
- Web Tension
- Line speed
- Dirty ground roll
- Damaged roll covering
Free Offers
And of course, when it comes to surface treating, “cleanliness is next to godliness”. If you don’t have a cleaning program in place, start one today. Our free Maintenance Planner is a great way to start up a program or refine your existing one.
In the meantime, if you’re still having problems with backside treatment, send us a sample and we’ll evaluate it for free. We’ll test it in our lab with a variety of systems including our Universal Roll corona treater which is designed to minimize any chances of backside treatment. And if your application requirements specify a zero-tolerance for backside treatment, we’ll run your material through our Plasma3™ atmospheric plasma treater which can completely eliminate backside treatment.