Flexo Ink Adhesion & Surface Treatment Insights
So, do you think you know everything there is to know about surface treatment? Well, let us pose a few questions to test your IQ on this subject:
- LDPE film is corona treated. One portion of the film is left exposed to air, and another portion is protected from exposure to light, moisture, air and dust. Printability is evaluated for each based on print density, dot gain and mottling. Which corona treated films had the better overall print quality?
- Paperboard is coated with SB co-polymers to improve flexo printability and barrier properties. Corona and atmospheric plasma treatments were applied separately and flexo print quality evaluated. Which surface treatment process provided the best print quality without sacrificing barrier properties?
Before you search for the answers within this article, let’s explore some other surface treatment tenets you might find revealing. First, when we talk about surface treatment, what are we considering by definition?
Water-based & Solvent-based Ink Adhesion
Surface Treatment – the act of modifying the surface of a material to change the physical, chemical or biological characteristics originally resident on the surface of a material.
Surface treatments have been effective for many years in modifying substrate surface characteristics to promote the adhesion of flexographic inks films and papers. For papers, the partial absorbency of water-borne and solvent-borne inks into the substrate (and partial vaporization) is key for adhesion. However, the printing of water-based inks on a non-porous film or foil cannot rely on absorbency and partial vaporization.
Unlike solvent-based inks where binders are dissolved in the ink solvents, flexographic inks use binders which are not soluble in water. Specifically, they are primarily composed of a styrene acrylic alkali-soluble binder and a resin emulsion. The alkali-soluble binder dissolves in alkaline water, which contains ammonium hydroxide. This resin also is used to disperse the pigment. This binder has a large number of carboxylic acid sites and a relatively low molecular weight. The emulsion is a high-molecular-weight resin.
As the ink dries, ammonia and volatile amines leave the ink to allow the emulsion particles to “touch” and combine to form a continuous surface ink film. Waxes trapped in this continuous ink film will migrate to the surface. The movement of these waxes, plasticizers, and other ingredients takes about 24 hours after the ink film is dried. Higher temperatures increase the rate of migration. High humidity will cause the water-based inks to “dry” more slowly.
The Impact of Surface Treatment on Ink Adhesion
When the surface tension between the non-porous substrate and flexo ink is too great, modification of the substrate surface tension is required to aid ink transfer and adhesion. Specifically, if the substrate surface is not approximately 10 dynes/cm higher than the surface energy of the flexographic ink, the ink resin and binder will not sufficiently spread. For example, flexo inks typically have a surface tension of 35-38 dynes/cm. It is recommended therefore that the substrate surface tension be treated to 45-48 dynes/cm. To further optimize adhesion, chemical bonding can be improved by introducing more alcohol (COH) groups to the substrate surface by surface treatment.
Adhesion Effects of Slip Agents & Additives
Additional barriers to adhesion, particularly to films, involves high-load levels of slip agents (> 500ppm) and other components which provide the film the ability to glide more easily over conveying rolls during processing. However, these additives are, by design, formulated to be incompatible with the film. As such, they migrate in all directions from the interior of the film to the surface, creating a “weak boundary layer” to ink adhesion. This boundary layer of fatty acids needs to be removed so more of the native substrate surface is exposed.
Ink Considerations
It is typical for the addition of ink system vehicles to generate higher viscosity in water to therefore allow for lower resin solids. Higher viscosity will also form issues related to dot gain and dot bridging. However, too high a viscosity will impede wettability and reduce surface anchorage. Reducing ink viscosity in concert with increased surface tension by surface treatment will allow the ink to adhere better to the substrate. Also, paying close attention to the pH of the flexo ink will contribute greatly to ink transfer from the anilox cells and wet-out on the substrate surface.
Now let’s consider the trapping of flexo inks for a moment. We all know that print trapping is essential with certain graphic designs in order to compensate for minute misalignments between print stations. This is particularly true when challenging presses to impart high resolution graphics at high processing speeds. During trapping, if the wet-out of the first ink down is adequate, but the ink intended to be trapped does not wet-out properly, then it is highly probable that there will be insufficient ink drying and poor ink adhesion. These issues can manifest themselves with failed in-field performance, such as ink rub-off.
Did you know that surface treatment can improve the trapping of inks?
Its known as the “step technique”. The primary principle of the technique is recognition of the surface tension dynamics of substrate-to-ink and ink-to-ink. For example, if a polypropylene base substrate is corona treated from 29 mN/m to 42-45 mN/m to properly wet-out a flexo ink but the surface energy of the “skin layer” of the overprinted ink is not modified from its native state to wet to the base ink layer, there can be a high potential for ink picking.
The step technique applies steps of descending surface tensions from the substrate to the first ink layer, and from this one to the next, etc. In this way, proper adhesion of each ink layer to its support (or trap) is achieved. Insufficient trapping, i.e. inadequate ink adhesion because of incorrect surface tension, is therefore avoided.
To successfully surface-modify for optimal wetting, trapping and adhesion, accurate measurement of substrate surface energy is key. The use of dyne solutions (or dyne pens) is currently the predominant technique. The dyne solution technique is transferable to many materials.
Dyne Test Variables & Recommendations
If the test fluid permeates a porous substrate such as paper and causes swelling, surface energy results will indicate unrealistically easy wetting. Just as non-qualifying, a chemical reaction between the test fluid and the substrate invalidates results altogether.
To ensure test replicability, material preparation and test technique must be standardized. ASTM Standard D618 documents the suggested conditioning methods. However, this standard is untenable for treated film testing, since the material conditioning times range from 24 to 96 hours. These conditioning times may be of value for research and development purposes, but for normal quality control testing, much shorter conditioning times are commonly used. In this vein of thought, standardization of ambient, substrate, and test solution temperatures is critical, as is the inspection methodology.
It is recommended that one trainer be identified to instruct all surface energy testers to minimize measurement variability. Also, relative humidity should not be excessive since higher relative humidity will increase data variability. Finally, the elapsed time between extrusion or coating to surface energy test (or from this test to printing, etc.) must be controlled. Other advisable precautions with this test procedure include the following:
Avoid touching or contaminating the surface to be tested, as dirty surfaces lose their wettability.
- Avoid using contaminated test fluid; discard every 6 months
- Do not retest the same location on a sample
- Store and use all test fluids at room temperature
- Use fresh cotton swab applicators for each test
Did you know that dyne levels are often lower on an aging of substrate?
If the constraints of your process preclude good standardization of test timing, designed experimentation should be used to measure the effect of aging on your substrates. Substrate suppliers will typically set material specifications to conservative levels to compensate for treatment loss. Although surface energy is critically important to many converting operations, the topography of the substrate, coating rheology, and chemical incompatibility are just as critical.
Other important factors include the type of resin used for film or coating, the particular ink or adhesive to be used, surface roughness, and the interaction between the media and the reactive sites. By systematically measuring substrate surface energy, a starting point is established from which to resolve adhesion problems.
Surface Treatment Technology Options
Corona treatment is the most widely used surface treatment technology used by flexographic printers to control surface energy for successful ink adhesion. Bare and ceramic covered ground rolls are used in conjunction with high powered ceramic electrodes to generate the corona for these applications. Special pressurized systems are available for corona treating when printing with solvent inks as well. Most flexographic printers will incorporate a watt density controller to ensure the correct amount of treatment is applied to the film across varying line speeds.
In most cases, treating the entire width of the web is required. However some applications such as printing of stand-up pouches or bags require selective treatment as it is important to not treat the heat seal portion of the pouch. If the heat seal section runs across the width of the web direction a skip treat controller is used. The controller automatically turns the corona treater on and off at precise times to create treated and untreated areas of the web.
If the heat seal areas run the length of the web in lanes then a segmented treater is used. Metal electrode segments enable operators to select precise lanes for treatment and nontreatment. Pattern corona treating is more complex, but can be accomplished with a combination of skip treatment & lane treatment. This provides complete flexibility over the areas of the web which require treatment.
For printers not achieving the results they desire with corona, employing atmospheric plasma surface treatment is an option. Atmospheric plasma systems utilize unique gas chemistries to clean, etch and functionalize surfaces to produce results not possible with corona. Plasma treatment can produce higher and longer lasting results than corona treatment.
Pop Quiz Answers
Okay, it’s time to reveal the answers to the “pop quiz” posed at the beginning of this article
IQ Answers:
- This study was conducted by Behudin Mesic, et al. and examined the tendency for flexo ink to spread on the surfaces using contact angle measurements. Trials revealed that the surface energy of the protected sheets decreased with time, but not as much and not as quickly as that of the unprotected LDPE sheets. In the case of the protected LDPE film, the percentage of uncovered areas and mottling after printing remained constant, but for the unprotected sheets mottling increased with increasing time after the corona treatment. No significant differences were seen in the other print quality measures.
- This study by Thomas Schuman et al. indicated that intense corona treatment led to an undesirable increase in the WVTR value. A less intense corona treatment preserved the WVTR value to a great extent, but the flexographic printability remained unsatisfactory. With plasma treatment, the water vapor barrier was not impaired, and the flexographic printability of the plasma-treated dispersion-coated substrate was good.
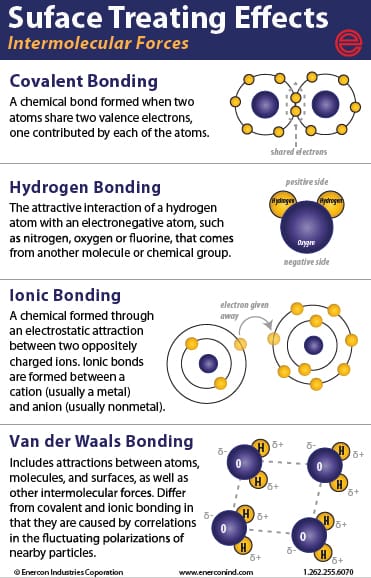