How Bump Corona Treating Improves Laminating, Coating & Printing
Whose responsibility is it to make sure a film is ready to be converted? Film supplier or Converter? Depending on what part of the world you are in this question can spark an inspired debate.
Both the film supplier and the converter are in business to make money. When printing, coating & laminating applications go wrong it’s a financial hit in either scrap material or in lost customers. So what’s a converter to do?
The tendency in emerging markets is for converters to reject film at the receiving door if it fails a dyne level test. And this is somewhat understandable. Many emerging market converters have no way of successfully converting film with low dyne levels. They expect their supplier to provide ready to convert film.
What mature market converters have come to recognize is that there are a number of factors outside the film supplier’s control and it is in their own best interest to take control of their process by adding “bump treating” into their standard process.
“Bump treating” refers to the installation of corona treater(s) on the converting line immediately prior to the application of inks, coatings and laminations. This “fresh” corona treatment provides converters with more control of their process. It enables them to overcome unexpected fluctuations in incoming film dyne levels and increases their operating window.
This article will review the factors that have driven leading converters in mature markets to take control of their processes by adopting “bump treating” as a standard best practice.
From Resin to Converted Product
To understand the differing views on this concept we need to follow the journey of a film from resin to finished product.
The whole concept behind surface treatment is to improve wettability and promote adhesion. When most films are extruded from resin their surfaces are non-porous and chemically inert with very low surface energy. Film extruders will corona treat their freshly extruded films to increase their surface energy. In fact, film’s that are not corona treated at the time of extrusion may never be receptive to future corona treatment.
Surface energy is commonly measured in units of measure called dynes. 1 dyne equals a centimeter-gram-second unit of force. Most converters will have a target dyne level range that works well for their specific process. While dyne levels do not guarantee adhesion, generally speaking higher dyne levels produce better adhesion results than lower dyne levels.
Why Dyne Levels Decay
The increase in a film’s dyne level is not permanent. In fact, dyne level decay and surface contamination are for the most part, out of the film extruder’s control once the roll of film leaves their facility. Some of the reasons for this include:
- Additives: additives are included in a film extrusion recipe for a variety of reasons such as enabling better film handling. When a film is freshly corona treated organic and inorganic contaminants are removed from the surface layer which actives the surface and increases its surface energy. Over time additives will migrate to the surface of the film which will diminish the effects of the corona treatment.
- Contamination: handling of the film or exposure to dust, debris or oils after corona treating can impart contaminants on the film’s surface
- Environment: high levels of humidity are known to accelerate dyne level decay
- Natural decay: even without additives, external contamination, or environmental factors dyne levels will decay over time. The precise level of decay will vary based on many factors including the specific substrate and original level of treatment. Under normal circumstances dynes levels will decay and eventually level off.
This should provide you with a good understanding of some of the reasons dyne levels will decay at a rate that is often out of control of the film supplier.
Potential pitfalls of dyne level readings?
As a matter of best practices most converters will spot check the incoming dyne level of films prior to converting. This is a recommended quality control procedure, but caution should be taken when interpreting the results.
Consistency: does your operation have a dyne level test that is consistent and repeatable? The most accurate results will come from a Meyer rod draw down test. Some companies use a pass/fail test with dyne pens which can be acceptable, but are subject to a greater variance in results.
Interpretation: is your staff properly trained in interpreting dyne level test results? It’s not uncommon for two highly trained people to interpret the same dyne level test with a margin of error of 1-2 dynes. The message here is that a difference of one dyne is not to be taken too literally.
Results: does your team understand what they are testing? It’s important to note that a dyne level test only tests one small portion of the film. There’s no guarantee that the entire roll of film holds the same dyne level. Furthermore dyne level is only an indicator of a film’s wettability and actual adhesion is dependent on additional variables including numerous process parameters.
Real world examples
Let’s compare two companies, Company ABC who has invested in a corona treater for converting and Company XYZ has not.
Scenario 1: Film arrives from a supplier with an acceptable dyne level, but is inventoried for several weeks prior to converting. The dyne level decays over these few weeks to the point that it cannot be converted in its current state. Company XYZ struggles with converting the film and ultimately fails to produce saleable product and making delivery. Meanwhile Company ABC has no problems converting the film as they “bump treat” it in line with great success.
Scenario 2: Historically the two companies have laminated film on a solventless laminator without the need for corona treatment. One day a roll of film appears to have irregular patterns of surface energy throughout the film. Again Company XYZ struggles with inconsistent results. Meanwhile Company ABC has eliminated the variable of surface energy and produces high quality products roll after roll.
What Industry Experts Say about Bump Treating
An instructor from a flexographic printing program says, “Films are pretreated, but they’re not guaranteed to be perfect when it comes time to print. Treatment degrades over time so that’s one issue you have to contend with. And, even if the film makes the grade on a dyne test you still have the possibility of additives rising to the surface. These surface imperfections can result in pinholing and other quality issues. A corona treater can help eliminate these problems.”
A Director of Engineering from a company that offers custom coating sees other benefits to bump treating, “There’s something to be said for a fresh treat. Dyne level does not always guarantee adhesion. Dyne level is simply a measurement of wetting-out. We’ve seen materials with equal dyne levels, one freshly treated and one from inventory and the freshly treated material consistently provides the better adhesion.”
While there are some applications that almost always require bump treating, such as many water based printing processes, you may be surprised to learn that many converters find benefits from bump treating solvent printing processes.
One solvent printing Operations Manager recently told us, “There’s no doubt that our lines with corona treaters have less delays and downtime. The treaters provide a safety net that assures surface dyne levels are optimal for printing.”
The Key is Taking Control
Education is key to ensuring both the film extruder and converter understand the relevance of dyne levels, the role of corona treatment and the expectations that they should have for each other. The film supplier strives to supply pretreated film within a dyne level range that can be converted. The converter should take responsibility for converting that film and do their best to eliminate surface energy as a variable by employing a corona treater to bump treat films prior to converting.
As emerging markets become more experienced with these applications issues they will be more likely to take a leadership position in their market by employing the lessons learned from mature markets.
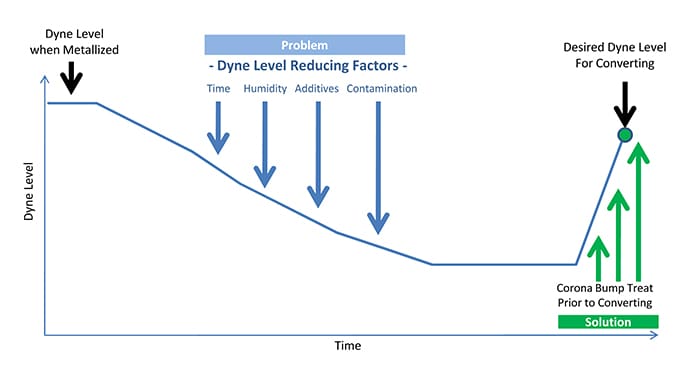