Do roll coverings add cost or value? Get the facts.
One of the most common questions asked by film extruders and converters is which roll covering is best for their application. You might be surprised at the variety of choices when it comes to selecting a roll covering.
In this article, we’ll provide the basic facts about four types of roll coverings and then conclude with some application information that may affect your choice.
Keep in mind ultimately the choice is yours. Some companies such as the Crayex Corporation elect to use a bare-roll system to eliminate the need to ever worry about changing a roll covering forty feet in the air.
Silicone Sleeves (350 to 400 in2/kW)
The most common roll covering is a silicone sleeve. These sleeves have good dielectric strength at 350-400 in2/kw which allows them to handle all basic corona treating applications. (Remember a lower rating allows you to direct more power at the roll.) For roll diameters greater than 8”, vulcanized silicone must be used.
Silicone sleeves are very economical and replaceable. The downside is they can be damaged from over exposure to corona or accidentally by the slip of an operator’s knife. While the cost of a new silicone roll covering is not great, costs from unexpected downtime and comprised product quickly add up. Life expectancy of a silicone sleeve is six months.
Epoxy coated rolls (450 to 500 in2/kW) Epoxy coated rolls offered a more durable covering than silicone and are also a good choice for basic corona treating applications. Epoxy coatings have harder surface than silicones or rubbers and many customers select the epoxy covered rolls as added insurance against unexpected roll failure from exposure to corona or accidental operator inflected damage from an operator’s knife. A pinhole in an epoxy roll can be field repaired. Life expectancy of an epoxy covered roll is one year.
Ceramic Covered Rolls (250 to 300 in2/kW)
Ceramic covered rolls provide a dielectric strength of 250-300 in2/kw. These rolls are ideal for high speed and demanding corona treating applications. They also offer exceptional durability with a two year limited manufacturer’s warranty. And unlike other roll coverings most repairs can be accomplished in the field. Usually the initial cost of a ceramic covered roll is greater than a silicone covered roll, however the costs can be closer than you might think. Since ceramic covered rolls handle more power, a smaller diameter roll can often be specified. An added benefit of a smaller diameter roll is its ability to easily handle thin gauge film. Because of these application benefits a cost comparison over the life of the station can work out favorably for a ceramic roll covering.
Glassed-steel rolls (200 to 250 in2/kW)
These rolls provide the highest dielectric strength at 200 in2/kw According to the roll covering supplier these coverings provide an energy savings because of their high efficiency which results in improved treatment levels. In most cases the roll diameter for a glassed-steel roll will be smaller than comparable roll coverings.
Retrofitting roll coverings
Changing the type of roll covering you currently have could benefit your operation. However you need to consult with your surface treater manufacturer to determine how a change in roll covering may affect the rest of the surface treating station. For example, if your change in roll covering results in a downsizing of your roll diameter, you’ll need to determine the effect of the geometric relationship of your electrodes and new roll. You may or may not have enough latitude in the mechanical framework of the treater to correctly position the electrode relative to the new roll diameter. On new installations it is always best to consult with both your primary OEM and your surface treating supplier directly.
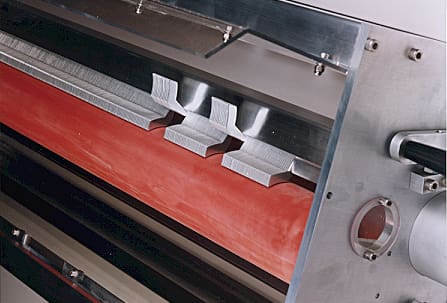