Clearing the air on the gap between ceramic coated ground rolls and their bare roll predecessors.
Years ago, corona treating technology was pretty simple and straightforward. There were two types of corona treating systems to choose from: Covered Roll systems and Bare Roll systems. Since that time ceramic coated ground rolls have revolutionized bare roll systems.
These systems have become popular because they provide more power than their predecessors and also eliminate common problems associated with covered rolls. While the cost of a new silicone roll covering is not great, many companies are realizing there are more costs associated with replacing them than just the cost of the new sleeve.
Consider the following scenarios. Your silicone covered roll becomes damaged from either over-exposure to corona or because it was cut with a knife. If the damage is severe enough, you’ll know right away because it will cause a high voltage trip. That will cause you to shut down the line, most likely during an important run, and replace the roll covering.
But what if the damage isn’t enough to cause a high voltage trip? In this case, your substrate could be experiencing pinholing or backside treatment. These two problems are often difficult to detect and will certainly compromise your product’s quality. And you might not learn of the problem until your customer complains that your last delivery isn’t up to par. By this time, you may have produced several hundred-thousand feet of sub-standard material. You’ll have to deal with excessive scrap, customer complaints, and you’ll still lose production time when you shut down to replace the roll covering. So, you can see that the costs can quickly add up to more than just the cost of the roll covering.
So what are the rules of treating with the new wave of Universal Roll treaters? First let’s start off with definitions of the terms ceramic covered rolls, conductive ceramic coated rolls and Universal ceramic coated rolls.
Ceramic Covered Rolls
These rolls are covered with a thick ceramic covering (0.060″ to 0.100″) that is applied via a plasma-spray technique. This roll covering replaces the rubber or epoxy coverings used with metal electrodes. The purpose of the roll covering is to provide a dielectric buffer between the metal electrode and the roll covering allowing the air to ionize to create the corona in the air gap. Ceramic roll covering is widely used because of its high dielectric strength and resistance to physical damage. This type of electrode / roll combination cannot be used to treat conductive films.
Conductive Ceramic Coated Rolls
Conductive ceramic is a thick coating (0.002″ to 0.005″) that is applied via a plasma-spray technique. This coating is used on bare roll systems where ceramic electrodes are utilized. The coating protects the ground roll from oxidation (corrosion). This covering replaces chrome or electro-less nickel plating which are porous and will allow oxidation between the roll core and the plating.
From an application standpoint, a conductive ceramic coated ground roll in a bare roll system is recommended when treating metal foils or the non-conductive side of conductive films. The conductive ceramic coating ensures a conductive path to ground from the conductive web surface. Please keep in mind that the primary benefit of the conductive ceramic is to prevent oxidation and other damage to the roll surface.
Universal Ceramic Coated Rolls
Universal ceramic is also applied to the roll core via a plasma-spray process. The universal ceramic coating is non-conductive and also serves as a dielectric covering on the ground roll. This roll coating is used in systems utilizing ceramic electrodes. Although the universal ceramic coating is non-conductive, it is unlike the ceramic coating used with metal electrodes. In fact, the universal ceramic is NOT to be used with metal electrodes.
“Did you know that Enercon offers a conductive ceramic roll station that is ideal for metallized film and foil?
So, can one use a universal ceramic-coated roll system to treat metallized films or foils? The answer is “yes”. How is this possible?
Since both the high voltage electrode and the ground electrode (ground roll) are covered with a dielectric, the corona will be established in the air gap between the electrode and metallized film or foil. However, it is important that the metallized surface of the film be in contact with a clean and grounded idler roll. This idler roll can be covered with conductive ceramic to prevent oxidation and provide a ground path from the conductive film surface.
The advantages of using universal ceramic-coated roll system verses bare-roll system are:
- Superior treatment levels
- The elimination of film wrinkling or puckering
- The elimination of backside treatment
- The elimination of pin holing on the metallized surface
Universal roll compared to silicone covered: While the initial cost of a ceramic covered roll is greater than a silicone covered roll, it can cost less over the life of the station. It is important to note that in some cases the initial costs are very close. The higher efficiency ceramic covered roll requires less power to meet the same treat requirements, therefore reducing the cost of the power supply required.
I hope this clears the air regarding your ceramic options. Please contact Enercon if you have any comments or questions. We would like to hear from you.
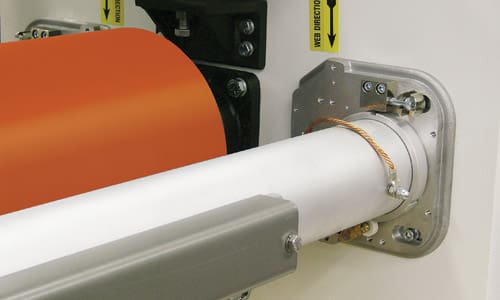