Flexible Extrusion Line is a Novel Idea
What does an already-successful converter do when Opportunity knocks?
If healthcare customers are at the door, and they’re asking for high-barrier packaging capability that you don’t have enough of, you’d better get it. And that’s exactly what Amcor Flexibles Madison, WI did.
In 2001 the company, then Rexam Healthcare Flexibles, undertook an aggressive plant expansion of over 60,000 sq.ft. and installed a unique tandem mono and coextrusion line from Black Clawson.
The ISO 13485-registered plant boasts capabilities that have it well-positioned to take advantage of the market growth in healthcare packaging.
New capabilities reduce lead time and costs
The line is unique in that it can be operated as two separate lines or as a single line through the use of a web bridge. As a tandem line, it produces complex multilayer structures. Bob Liesenfelt, product development manager for coated and laminated products, says, the new capabilities “reduce lead times, allow us to better control costs, and continue our commitment to innovative products.”
Innovation is key as film producers attempt to keep pace with the requirements of their customers for moisture/oxygen barriers and active packaging. John Ozcomert, PhD, director of technology at Amcor Flexibles Madison, says the company made an investment for the long haul. “It’s incumbent upon us as market leaders to invest in technology that allows us to exploit new materials and novel structures. This line allows us to do just that.”
The facility is now able to produce high-tech laminates for the healthcare industry, including various peelable laminates, extruded and coextruded multilayer constructions, and multilayer blister webs using tie layers.
A big project
The company relied on Black Clawson for turnkey responsibility for the rest of the project. The term turnkey is sometimes carelessly tossed about by manufacturers and customers. For Amcor it meant that Black Clawson would not only have responsibility for the installation but would oversee the installation of ancillary equipment from OEMs.
Says plant engineer Doug Enders, “We minimized our risk and were confident with the excellent OEMs that teamed up on the project that there wouldn’t be any finger pointing if the going got tough.”
Those OEMs included some of the industry’s best. Process Control handled the silo erection and resin conveyance, NDC supplied the film gauging system. Eurotherm provided the systems’ drives. The guiding system was built by Fife. Enercon provided six treaters–one primary, two secondary, and three post-treaters.
Ray Whitmore, Black Clawson’s director of project engineering, cites the cooperation of the expert suppliers brought in on the project as critical to the success of the project. “A lot of times the difference in the equipment isn’t as large as the difference in the companies supplying the equipment.
Take Enercon for example: along with the other companies that supplied equipment on this project, they provided extended training programs for the Amcor team. All of the organizations involved support their products in a highly professional manner and that makes bringing the project together much easier.”
Each of the suppliers of the ancillary equipment provided technology and system training that proved crucial to the success of the final project. Enercon provided three corona treaters for each line. The first two each treat the substrate to raise substrate surface energy for laminating adhesion. The final treater treats the finished product to raise surface energy for additional converting, such as printing.
NDC Infrared Engineering provided beta-transmission film-thickness gauging systems . The installation of this type of gauging system is a measure of just how critical the consistency of the extrusion is to the specifications demanded by healthcare customers. The line is now turning out constructions for the healthcare and personal-care markets, enabling the converter not only to compete economically but, as Ozcomert puts it, “make novel structures.”
“We are continually meeting new performance requirements from our customers,” he says, “from UV, moisture and oxygen barriers, to active packaging and moisture and odor barriers. In addition, they demand quick turnaround, high capacity, and a clean manufacturing environment for their materials. We’re able to give them that.”
Says Liesenfelt, “In the healthcare market, it is important for our customers to know that we understand the regulations they’re dealing with, that we are not taking any shortcuts, and most of all that we understand the literally life-and-death nature of their products and the way they are used. Operating this way is how we will continue to be leaders in this market.”
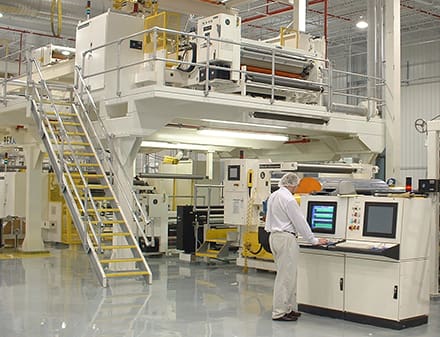