Eagle Film Extruders Soar High with an Eye for Detail That Ensures Flat Film Production
Eagle Film Extruders, Inc. (Grand Rapids, MI) goes to great lengths to produce the “flattest” film possible. As an ISO 9001:2000 certified company, it only uses prime-grade resins and state-of-the-art equipment to create consistent, flat film.
“Our customers want the complete package,” says George Collins, Eagle president. “They don’t care how it gets done, only that we have met or exceeded their expectations every time. We could make the flattest and most consistently blended film in the world, but if we did not surface treat it to specification, label it correctly, package it securely or deliver it on time, we fell short. The intangibles, more than ever, are also noted as a very important key to our success.”
In order to meet customers’ expectations, Eagle takes great care in controlling every detail of the film-making and film-treating processes. Not leaving anything to chance, the company even stores its resin silos inside the plant. This way, the plastic resins are not affected by changes in the weather.
Craftsmanship and computers
Once the resins make it to either the monolayer or the three-layer Windmoeller & Hoelscher Corp.’s VAREX blown film extrusion lines, the blending of the resins and the making of the film are completely controlled by computer.
“Although there is still craftsmanship involved, we wanted to move Eagle into the realm of science and away from the traditional art method of producing blown film. Computerizing our process has allowed us to do this successfully,” says Len Fouty, Eagle vice president.
The extruder features an automatic die control with a capacitive thickness gauge. “From set-up to finish the computer is minutely controlling every facet of production; blend, width and thickness come into control quickly improving up-time and reducing scrap. Our customers, in turn, benefit from a very high level of consistency, whether it is a 300-lb. trial or a 200-roll order, the film will process in their equipment identically from the sample stage throughout future production runs. Manual systems are not capable of providing film with this type of consistency,” Fouty explains.
Flat film equals consistent treat
Eagle aims for the flattest film not only for its customers’ applications but for its own treating process as well. “Flatter film allows us to precisely target in on a specified dyne level and hold it uniformly across the entire web,” Fouty says.
Along with cutting-edge extruders, Eagle made sure to install treaters that matched their flexibility without compromising quality. “With very little limitation, we have been able to produce the stiffest and softest films from 0.6 to 18 mils in thickness. We needed a treater that would not limit our ability to produce these films. Enercon was able to provide us a treater solution that could meet this challenge,” Fouty says. Eagle has a two-sided Enercon covered roll surface treater with stainless steel electrode segments on each of the W&H systems. The segment sides are milled on a slight angle to help eliminate weak or missing treat lanes and they are also milled to match the curvature of the roll. “This increases the treatment dwell time and allows for more power to be dissipated into the film,” Collins says.
The treaters are powered by Enercon’s Compak™ 2000 power supplies which are able to provide full treatment across the length of the electrode consistently at very low and high speeds. “The turn-down ratio of these units add to the flexibility of our line,” Collins adds.
Just “being better”
But Eagle goes beyond just making sure its machinery and components are at top-form in order to provide its customers with the best film it can make. In December 2002, Eagle was approved for its ISO 9001:2000 certification, which means that the company meets the requirements for a quality management system.
“There’s no doubt about it; the level of support that is needed to continue forward with the ISO quality system is tasking on an organization. You have to be very dedicated to doing it; you have to believe in it. We believe that premium price for high-end equipment and added expense needed to keep up with the quality management system will translate directly into value for our customers. You can never lose sight that our customers have a choice; we have to continually raise the bar and strive to be the better one. We must provide better products, better quality, better service, better, better, better,” Collins says.
A commitment both to producing the highest quality film and maintaining the ISO quality system have combined to help Eagle build solid relationships with their customers. “More and more converters are investing in high-tech printing, coating and lamination equipment and they can’t always enjoy the benefit of their purchase if they have inconsistent film quality,” Fouty says.
“We have had many customers who tell of similar experiences. They may be accustomed to certain set-up times and line speeds using other films, however when using our film, they’re able to reduce set-up and ramp-up lines speeds over time with roll to roll consistency. There’s payback for them, which translates into value, which allows us to build upon our relationships.”
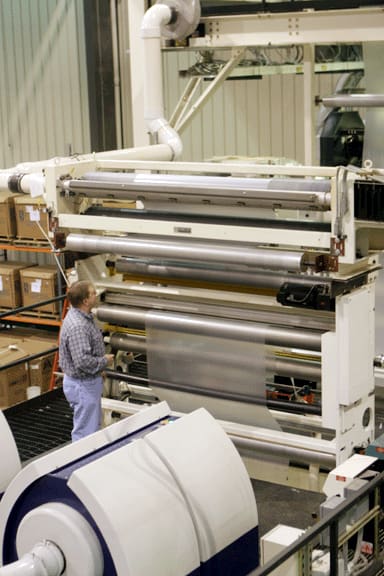