Dow Develops New Resin Technologies with Versatile Corona treating
The Dow Polyolefins and Elastomers (PO&E) Technical Service and Development Group recently invested heavily in its laboratory capabilities via a new extrusion coating and lamination line. Located at the group’s R&D headquarters in Freeport, TX this multi-million dollar line, supplied by Black Clawson Converting Machinery LLC (Fulton, NY), enables Dow engineers to develop and evaluate new resin technologies, as well as provide fast resolution of day-to-day technical issues for customers.
The Black Clawson line begins with two dual-direction unwind stands, each capable of handling rolls up to 3,000 lbs. and 60 in. diameter. An auxiliary unwind for lamination accommodates 1,200-lb. rolls up to 40 in. diameter. Coating and laminating widths of 15-30 in. are possible, and a turret rewinder provides finished rolls up to 40 in. diameter. Dual-range sensors throughout the entire line provide tension control for anything from thin films to heavy paperboard.
Creating tomorrow’s substrates
Extrusion coatings and laminations play a significant role in today’s package designs. Variables such as hot-tack and heat-seal strength, seal integrity, resistance to aggressive products, the ability to seal through contaminations, adhesion and cost can make an enormous difference when selecting a resin for packaging needs. Dow’s new line has been designed to help package makers better understand these variables and their effects on package designs.
The line is also used for new material development and to support ongoing advances in extrusion-coating technology. Specifically, Dow’s engineering team investigates the performance of new resins, chemistries, multiple substrates, and melt draw-down characteristics.
Getting real-world results
According to Dow project manager Jim Cooper, it’s important that Dow is able to accurately replicate real-world processing conditions. Because it incorporates the latest extrusion-coating technology, the line generates performance data and samples that converters can use to develop new structures. All Dow extrusion-coating polymers are supported by the new line, including DOWLEX linear low-density polyethylene, AFFINITY polyolefin plastomers, PRIMACOR copolymers, DOW low-density polyethylene, Saran barrier resins and new INSPIRE performance polymers.
The versatility of the new coextrusion coating line is further enhanced by two Universal roll corona treating systems from Enercon Industries Corp. (Menomonee Falls, WI). The 30-in. stations use ceramic-electrode technology and are engineered to treat any web material, including paper, film, and conductive foil/metallized film.
Cooper says selecting Enercon was an easy choice. “Over the last 10 years, our Enercon treaters have had outstanding reliability; in fact, they’ve never been down,” Cooper says.
The first treating system improves the quality of the extrusion by pre-treating the web prior to the extrusion process.
The second unit performs post-treatment, enabling converters to use the substrates for further value-added processes such as printing, embossing or hot-stamping.
The coextrusion line also includes a three-layer FGe feedblock and EBRe edge-bead reduction die from Cloeren, Inc. (Orange, Texas), for enhanced flexibility.
Cooper says, “The line’s flexibility enables Dow to not only develop new resins, but is a key factor in the company’s customer support operations. If a customer encounters a substrate problem, we can replicate their scenario on our line, evaluate it, and develop a solution for their requirements.”
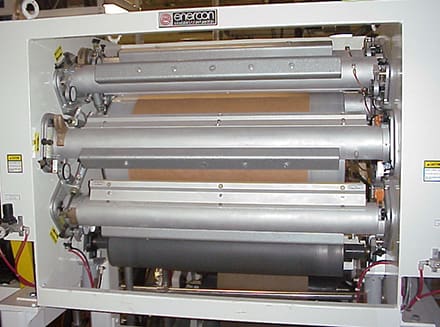