Corona Treating And The Solvent Printing Process
There are a number of external pressures on the converting industry which are increasing the need for surface treatment of substrates before printing. Printing on polyfilm or metallized films and foils instead of paper presents many production challenges. In addition, competitive pressures are pushing converters to produce a higher quality product at ever increasing line speeds. These factors contribute to the increasing use of the corona treating process before printing. The key factor in this equation is the difference in surface energy between the fluid vs. the substrate. If the surface energy of the ink is higher than that of the substrate, it will not “wet out” and the resulting adhesion and print quality will be poor. Solvent-based inks have a relatively low surface energy and in many cases are used on a variety of pretreated substrates.
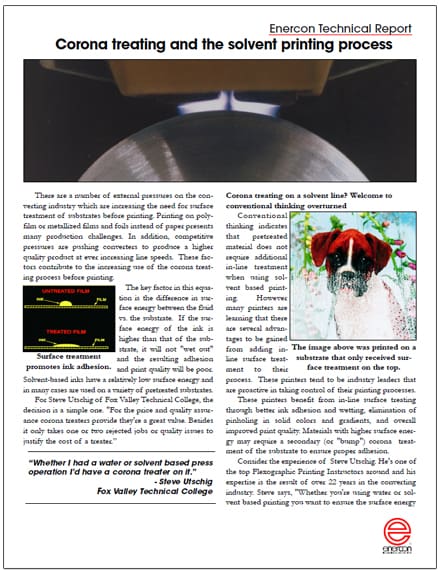