Lofton Label Reaches Lofty Heights with the Help of Surface Treaters
How do you earn the trust of a company for label runs in the millions? How can you confidently promise to deliver the job in a matter of a couple of days? Ask Lofton Label’s Production Manager Mike Gaughan and he’ll tell you its not only a matter of trust, it’s a matter of quality.
“Our key to delivering quality products is based on our investment in top of the line equipment. New technology allows our people to deliver high-end jobs with fast turn-around,” says Gaughan. At Lofton Labels’ facility in Invergrove Heights, Minnesota, Gaughan is responsible for a dozen press lines. Their capabilities include two-sided printing and they handle everything from paper labels to unsupported film labels, to bags and pouches. It operates 12 presses with sizes from 7.5″ to 24″ and with print capabilities from one to ten colors for film and up to 12 colors for labels.
They convert a wide range of material into a variety of high performance labels for the health and beauty, food, and general manufacturing markets, including primary labels, tags, and custom folded coupons. Its flexible packaging products range from pharmaceutical and nutriceutical packaging to recloseable pouches and dog food treats.
Materials range from 50-gauge BOPP for wraps to 4-mil LDPE with inline laminating of a 50-gauge PET for gusseted, stand-up pouches. Primarily, the company uses water-based inks, laminated with a heat seal film to sandwich the print. It also has UV ink capability for printing recloseable pouches.
Converting such a wide array of materials requires Lofton Labels’ production team to continually evaluate their presses and ancillary equipment. “Our key to delivering quality products is based on our investment in top-of-the-line equipment. New technology allows our people to deliver high-end jobs with fast turnaround,” says Gaughan.
The company not only frequently purchases new presses, but it also relies on upgrading press accessories to enhance productivity. High-quality anilox rolls from Praxair, video inspection equipment from BST Promark, and corona treaters from Enercon all help Lofton Label deliver high-quality products. The corona treaters have been an especially productive enhancement according to Gaughan. The company purchased two, 24″ Enercon Universal Roll Treaters (one two-sided and one single sided) through Dotray and Associates.
The treaters are capable of treating metallized and non-metallized substrates. It also has one Enercon narrow web 18″ two-sided treater. “We treat our entire flexible packaging material in-line, and also some supported film for pressure sensitive labels when needed, ” he explains The treaters have enabled Lofton Label to offer its customers a greater range of products. Additionally, primers have been eliminated in some cases with the use of corona treating, which Gaughan believes is a more reliable and cost-effective method of surface preparation than using primers.
According to Gaughan, there were several reasons that Lofton Label chose the Enercon corona treaters. On another press a corona treater is used to pretreat film and a second treater is used prior to lamination. One of the main reasons was the ease of cleaning the electrodes. Other factors included the exhaust placement on the treater and how easily the treater can be threaded up.
With the company’s emphasis on short-run, quick turnaround production, the accessibility of the electrodes for cleaning was a major benefit. “The biggest improvement was in cleaning during and after treating metallized material,” says Gaughan. “Our old treater took up to two hours to take out the electrodes and clean and reassemble them. Now we can clean the electrodes in a matter of minutes.” And productivity improvements like that help keep Lofton Labels growing.
Portions of this article also appeared in a past January issue of Package Printing.
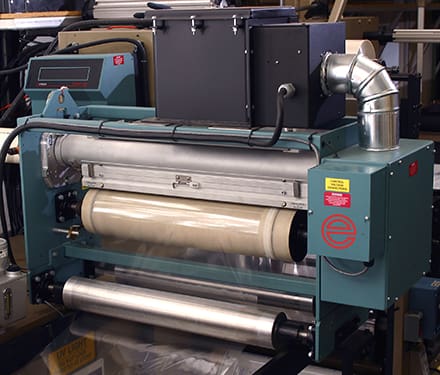