Cómo lograr un sello perfecto cada vez
Los productos que se encuentran perfectamente sellados brindan confianza al consumidor en cuanto a su calidad y seguridad.
Los fabricantes saben que un sello de mala calidad en sus productos no sólo amenaza la percepción del consumidor acerca de su compañía y sus productos sino que también resulta en pérdida y daño de los mismos durante el traslado.
El hecho de comprender como identificar y controlar las variables del sellado por inducción ayuda a lograr un sellado perfecto.
El proceso de desarrollar una solución de sellado perfecta incluye que se den las condiciones de compatibilidad entre la tapa, el sello (liner) y la selladora; que se ajuste una ventana de operación y el establecimiento del método de comprobación para identificar un buen sello.
Compatibilidad de Materiales
Se puede lograr un sello perfecto con cualquier tipo de envase.
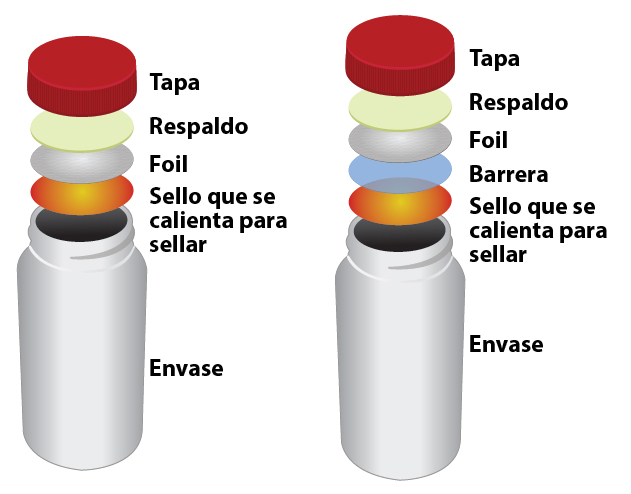
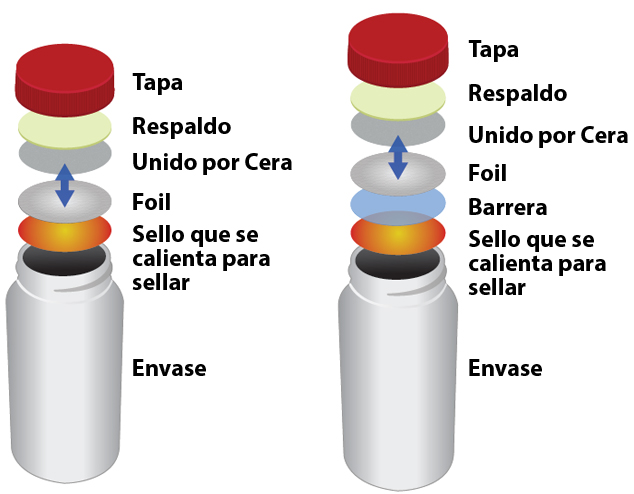
La elección del sellado por inducción apropiado depende del producto que se quiera empacar. Si el producto contuviera algún ingrediente volátil o potencialmente agresivo, químicos, ácidos, solventes, de alto contenido en sodio, alcohol o vinagre puede ser necesario un sello con una capa o barrera protectora, la misma puede ser ubicada entre el film que se calienta para sellar y el foil a fin de prevenir la corrosión.
El liner es la próxima consideración. Un tipo de liner es aquel de una sola pieza, el cual posee un respaldo comúnmente de cartón, espuma o una capa de papel. Cuando se realiza la inducción la estructura completa se sella a la boca del envase sin dejar nada en la tapa.
Este tipo de liner suele utilizarse para alimentos, bebidas y vitaminas o para productos que no requieren de otro sello en la tapa para sellar el producto una vez que el foil ha sido removido.
Otra clasificación es el liner de dos piezas. Este es un material de dos piezas unido por cera, el cual posee un respaldo usualmente de cartón o espuma unido al aluminio con cera. Durante el proceso de inducción la cera se calienta, se derrite y es absorbida por el respaldo, el cual permanece dentro de la tapa y permite que el producto quede sellado al cerrar el envase una vez que el aluminio ha sido removido. Cuando se trabaja con productos agresivos o volátiles puede incluirse una capa que actúe como barrera entre la capa que sella por calor y el foil.
También existe un sello de dos piezas que combina una barrera de mayor contención y el sello de aluminio. El respaldo de este sello posee una lámina de poliéster con el fin de proporcionar mejor permeabilidad de oxígeno y mejor transmisión de vapor o humedad una vez que el sello haya sido removido.
Finalmente se deben determinar las características de remoción del sello. Su aplicación necesita de un sello que al ser removido no deje residuos del mismo en la boca del envase? Su producto requiere un sello que se suelde a la boca del envase o que deje evidencia de violación teniendo que destruirlo al abrir el mismo? O requiere un sello de fácil acceso, el cual puede abrirse oprimiéndolo con un dedo o cuchillo?
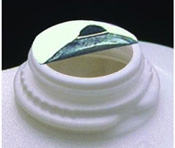
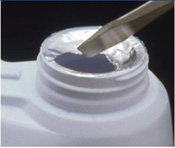
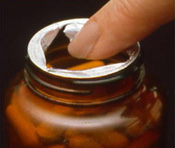
Selladora por Inducción
Para seleccionar la selladora por inducción apropiada para alguna aplicación en particular deben considerarse algunas variables. El diámetro del sello es una de las variables más importantes para medir el equipo. Un mayor diámetro de foil requiere una cantidad de energía diferente de la que requiere un diámetro menor. Como existen diferentes tipos de sellos y dependiendo de su espesor, éstos pueden calentarse en diferentes cantidades de segundos por lo cual es esencial registrar el tipo de sello para cada aplicación.
Asimismo, resulta de vital importancia conocer la velocidad de línea, preferentemente en metros por minutos. Si los envases pasan, es decir, se transportan demasiado rápido, no estarán demasiado tiempo debajo de la selladora, entonces se necesitará un equipo más potente. Si la única información disponible es el número de envases por minuto, deberá determinarse el espacio entre los envases para realizar un cálculo más preciso.
La geometría de la tapa y del envase constituyen consideraciones adicionales a la hora de seleccionar el cabezal de sellado óptimo para la aplicación. Existen diferentes tipos de envases y de tapas, y la mayoría de ellos pueden ser sellados con un cabezal de sellado plano. Sin embargo, algunos envases tales como los que poseen tapa deportiva, tienen una separación demasiado grande entre la boca del envase y el sello de inducción, razón por la cual se requiere un cabezal de sellado especial.
Además, deberá determinarse el rango de aplicaciones. Si se debe sellar un amplio rango de envases o tapas, el equipo deberá ser configurado de acuerdo a la tapa del envase, al envase propiamente dicho y a la velocidad de sellado.
Una vez que se haya documentado toda la información, se podrán elegir las opciones más apropiadas de fuente de potencia y cabezal de sellado que se encuentren disponibles en el mercado. Para las tapas de diámetro más pequeños, el cabezal tipo túnel suele ser el más eficaz. Para las tapas deportivas, el cabezal tipo túnel profundo suele ser el más efectivo. Para aquellas tapas de más de 53 mm de diámetro, la mejor solución la aportará el cabezal plano. Si la aplicación incluye una amplia variedad de tamaños de tapas lo mejor será optar por el cabezal de sellado “all – in – one” (todo en uno).
Ventana de Operación
Una vez que haya seleccionado la tapa, el sello y el equipo de sellado por inducción deberá continuar hacia el siguiente paso: ajustar una ventana de operación para la selladora.
Una ventana de operación le permite obtener un rango de sellado óptimo, registrando rangos de sellado en donde no se logra sellar el producto, se logra un sello parcial, un buen sello y un sello sobrecalentado.
Esta información es muy importante ya que proporciona las bases fundamentales para cada aplicación en particular.
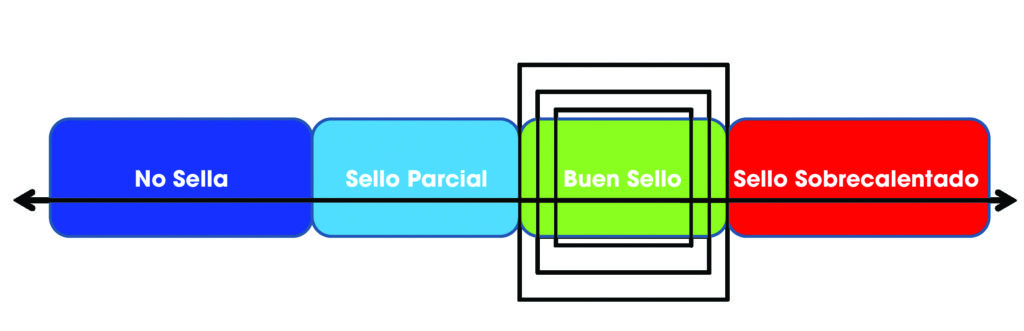
Paso 1: Asegúrese que el cabezal se encuentre correctamente orientado y alineado. La separación entre el cabezal de sellado y la tapa debe ser consistente. Es también importante asegurarse que el paso de los envases esté controlado, pues las botellas deberán pasar por debajo del centro del cabezal de sellado o por debajo de un cabezal pivoteado, basado en las especificaciones del fabricante.
Paso 2: Verifique las variables incluyendo la velocidad de la cinta transportadora, la cual deberá poseer un valor fijado con anterioridad, para obtener un mejor resultado (si la operación requiere sellar a velocidades de cinta variables, pregunte al fabricante de la selladora acerca de la Opción de Control de Sellado Variable). Asegúrese que las tapas y los envases sean compatibles, verifique que los mismos no tengan defectos de fabricación y compruebe que la torsión de las tapas sea consistente. Más del 80% de todos los problemas de sellado están relacionados con la torsión de las tapas.
Paso 3: Determine un punto de ajuste mínimo. Comience ajustando el porcentaje de salida al nivel mínimo de la selladora por inducción y, con todas las otras variables fijadas con anterioridad, haga correr un solo envase a través de la selladora.Compruebe que el envase haya sido sellado. Si no se ha logrado el sello incremente la salida en 5% hasta lograr un sellado parcial. Luego incremente la salida en 1 o 2 % hasta lograr un buen sello; este es el punto de ajuste mínimo de la ventana de operación.
Paso 4: Establezca el punto máximo de ajuste. Desde el punto mínimo de ajuste, incremente la salida de la selladora por inducción en 5% hasta que el sello o la tapa muestren signos de sobrecalentamiento. Luego disminuya la salida de la selladora por inducción en 1 o 2% hasta que los signos de sobrecalentamiento hayan desaparecido. Una vez que lo haya logrado, habrá determinado el punto máximo de ajuste de la ventana de operación.
Paso 5: Registre los datos. El porcentaje de salida para obtener un sello óptimo estará entre los valores de los puntos de ajuste mínimo y máximo registrados en la ventana de operación. Las variables que deben ser registradas son los detalles del envase, los detalles de la tapa, los detalles del sello, la torsión que se aplicó a la tapa, la velocidad de línea , la separación del cabezal de sellado y la salida de la selladora por inducción incluyendo el punto de ajuste mínimo, el punto de ajuste máximo y el punto de ajuste óptimo (cuyo valor que se encontrará en algún lugar entre el punto de ajuste mínimo y el punto de ajuste máximo).
Tamaño de la tapa (mm) | 15 | 18 | 20 | 22 | 24 | 28 | 33 | 38 | 43 | 48 | 53 | 58 | 63 | 70 | 83 | 89 | 100 | 110 | 120 |
Torsión (pulgadas/libras) | 6- 9 | 7- 10 | 8- 12 | 9- 14 | 10- 16 | 12- 18 | 15- 25 | 17- 26 | 18- 27 | 19- 30 | 21- 36 | 23- 40 | 25- 43 | 28- 50 | 40- 60 | 45- 65 | 50- 70 | 52- 73 | 55- 75 |
Como determinar un buen sello
Si bien no hay standares en la industria para comprobar la integridad del sello, existen varias maneras para determinar la calidad del mismo. Entre los métodos más efectivos podemos citar las pruebas al vacío, despachar / transportar el producto para comprobar cómo responde, sistemas visuales, presión mecánica, sacudir, apretar o pararse sobre un envase sellado.
Existen también ciertas características que, a simple vista, nos muestran que estamos frente a un buen sello, como por ejemplo un liner no decolorado, la adhesión a lo largo de toda la circunferencia de la boca del envase, un pliegue mínimo del sello y en los sellos de dos piezas, éste último no se encuentra oscurecido por sobrecalentamiento.
Resultará beneficioso poseer un proceso de diagnóstico basado en la información provista en este artículo para identificar y resolver cualquiera de los problemas referentes al sellado por inducción, ya que muchos de ellos pueden ser evitados estableciendo procedimientos de control de calidad en las tapas y envases, controlando el clima de almacenamiento, realizando inventarios, etc.
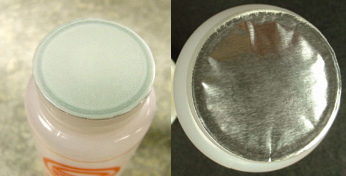
Un buen sello muestra adhesión alrededor de la boca del envase, no presenta decoloración y puede presentar un mínimo pliegue.
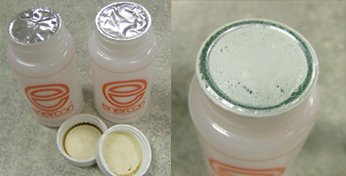
Un pliegue excesivo del sello, signos de sobrecalentamiento o la decoloración ya sea del sello o de la tapa, indican que el porcentaje de la salida de potencia está ajustado demasiado alto o que la velocidad de línea es demasiado lenta.
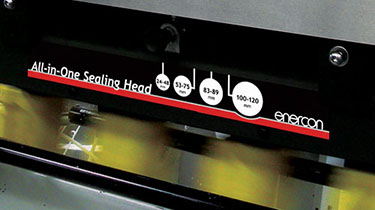