Purged surface treater safely allows solvent printers to run faster and reduce costs.
Solvent-based printers are recognizing the benefits of surface treating and Enercon has specifically designed a surface treater to meet their solvent printing needs. The system puts quality control in the printers’ hands by ensuring optimal substrate surface energy.
Materials with higher surface energy may require a secondary (or “bump”) corona treatment of the substrate to ensure proper adhesion. The results of surface treating are impressive.
Some solvent printers find they can run their line faster with a surface treater because of improved ink adhesion and wetting. Other printers find the elimination of pinholing in solid colors and gradients, and overall improved print quality reduces the number of returned jobs and operational costs. In both cases, the payback on the surface treater is fast.
Enercon’s purged stations are rated for safe operation in Class I, Division II, Group D locations. The “pressurized system” features positive pressure air-flow for safe operation in solvent areas. Doors on the system allow operators to access system components when the line is not in operation. Enercon’s power supplies with IGBT technology deliver reliable power to the system’s universal electrode station.
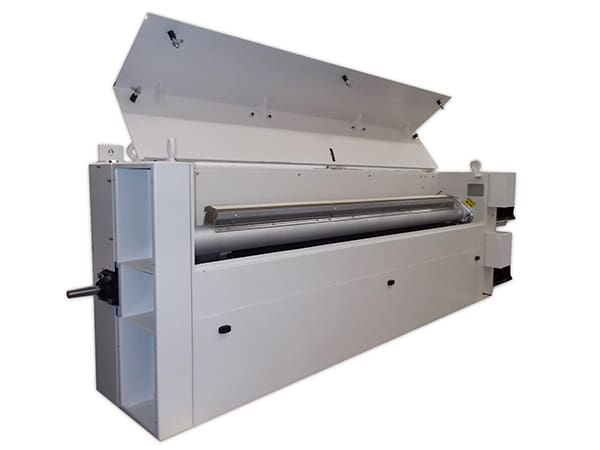