Can you use Watt Density to Predict Dyne Levels?
The ultimate goal of any surface treatment system is to increase surface tension measured in dynes which then increases the wettability and adhesion characteristics of the surface. This allows you to add value to the substrate through printing, laminating, coating etc..
Corona treating systems achieve this by applying a given level of power over a certain period of time to the surface. This power/time parameter is measured in watt density, which is defined as watts/ft2 (or m2)/minute.
Although watt density applied is directly related to increases in dyne level (surface tension), the relationship is not linear, and the relationship is dependent on system and material parameters.
System Parameters
Applied watt density is directly proportional to power supply size in watts and inversely proportional to station size(web width). Therefore if the web width is doubled the power supply must be doubled to maintain a required watt density.This simple relationship is complicated by two factors: line speed and the capacity of the electrode to handle a given level of applied power.
All electrodes, whether wire, metal bar, metal shoe or ceramic covered, have an upper limit on the amount of power they can accept per unit length. If, to achieve a given watt density, the power supply kW increases beyond the electrode’s maximum rating,either the electrodes need to be upgraded or additional electrodes must be added. Further, on a covered roll system an increase in the number of electrodes normally require an increase in treater roll diameter.
Line speed also complicates the sizing calculation. On a given system, the higher the line speed, the lower the maximum watt density that can be achieved. Being inversely proportional to watt density, line speed has a significant impact on system sizing and cost, which is why it’s important to properly define your application.
Watt Density Formula
Power Supply Output (watts)
Web Width(m) * Line Speed(m/min) * Number of Treat Sides
Material-Process Parameters
The most obvious material-process parameters are the basic substrate material composition and the process being performed (extrusion, extrusion coating, printing, etc.) Their impact on corona treating sizing is increasingly complex.
The tables included show immediate problems as most materials are defined by a range of typical surface tensions.The ultimate surface tension and amount of increase are dependent upon the material’s starting surface tension.
In addition some materials, such as some polyesters, accept treatment readily and exhibit rapid increases in surface tension under relatively low watt density levels, say 0.9 to 1.2. Other materials, such as polyethylene, accept treatment less readily but will exhibit a significant increase in surface tension under moderate watt density levels, say 2.0 to 2.5.
Finally,some materials, such as polypropylene, are difficult to treat and may exhibit only moderate increases in surface tension under relatively high levels of watt density, say 2.5 to 3.0. And untreated materials can be completely unpredictable.
So as you can see watt density is a valuable tool that must be balanced with system and operational parameters. And if you need a refresher on accurately determining dyne levels please see our tech paper on the topic.
Typical Watt Densities for Printing, Coating, Laminating | ||||
Solvent | Water | UV | Solventless | |
Pretreated LDPE | 1.5 – 2.0 | 2.0 – 2.5 | 2.0 – 2.5 | 1.0 – 1.3 |
Pretreated LLDPE | 1.5 – 2.0 | 2.0 – 2.5 | 2.0 – 2.5 | 1.0 – 1.3 |
PET | 1.0 – 1.5 | 1.0 – 1.5 | 1.0 – 1.5 | 1.0 – 1.3 |
Pretreated BOPP | 2.0 – 2.5 | 2.5 – 3.0 | 2.5 – 3.0 | 1.0 – 1.3 |
Note: Variations in resin blend, additives or process will affect values. |
Typical Treat Levels & Watt Densities | |||
Incoming Level | Desired Level | Watt Density | |
Treated BOPP | 34 – 36 | 40 – 42 | 2.5 – 3.5 |
Treated BOPET | 40 – 42 | 54 – 56 | 0.9 – 1.5 |
Treated LDPE, high slip | 34 – 36 | 40 – 42 | 2.5 – 3.5 |
Cast PP, no slip | 38 – 40 | 40 – 42 | 1.5 – 2.5 |
Untreated LDPE, low slip | 30 – 31 | need to test | need to test |
Note: Variations in resin blend, additives or process will affect values. |
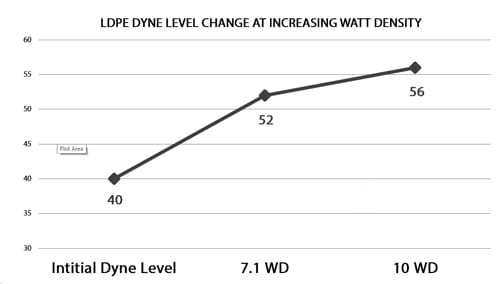